Devices
Industrial PCs / Embedded PCs
Out-of-the-box or customized Janz Tec industrial PCs have been developed in their robustness and reliability for industrial applications in various industries and environments. On this page you will find a selection of possible basic systems and configurations. Our team of experts will be happy to help you with individual requirements at any time.
ARM Industrial PCs
Embedded PCs
Compact Industrial PCs
Modular Industrial PCs
Rugged PCs
Rackmount Industrial PCs
Wallmount & Desktop Industrial PCs
Industrial GPU & AI Solutions
ARM Industrial PCs
Embedded PCs
Compact Industrial PCs
Modular Industrial PCs
Rugged PCs
Rackmount Industrial PCs
Wallmount & Desktop Industrial PCs
Industrial GPU & AI Solutions
ARM Industrial PCs
Our ARM Industrial PCs are compact and fanless systems that are perfectly tailored to your application. Based on Raspberry Pi or i.MX, they are not only energy-efficient, but also fully customizable – be it design or hardware. A variety of interfaces and scalable performance classes ensure that the systems can meet numerous requirements.
Here you can find a selection of possible basic systems and configurations.
Our team of experts will gladly assist you with individual requirements at any time.
Janz Tec emPC-A/RPI4
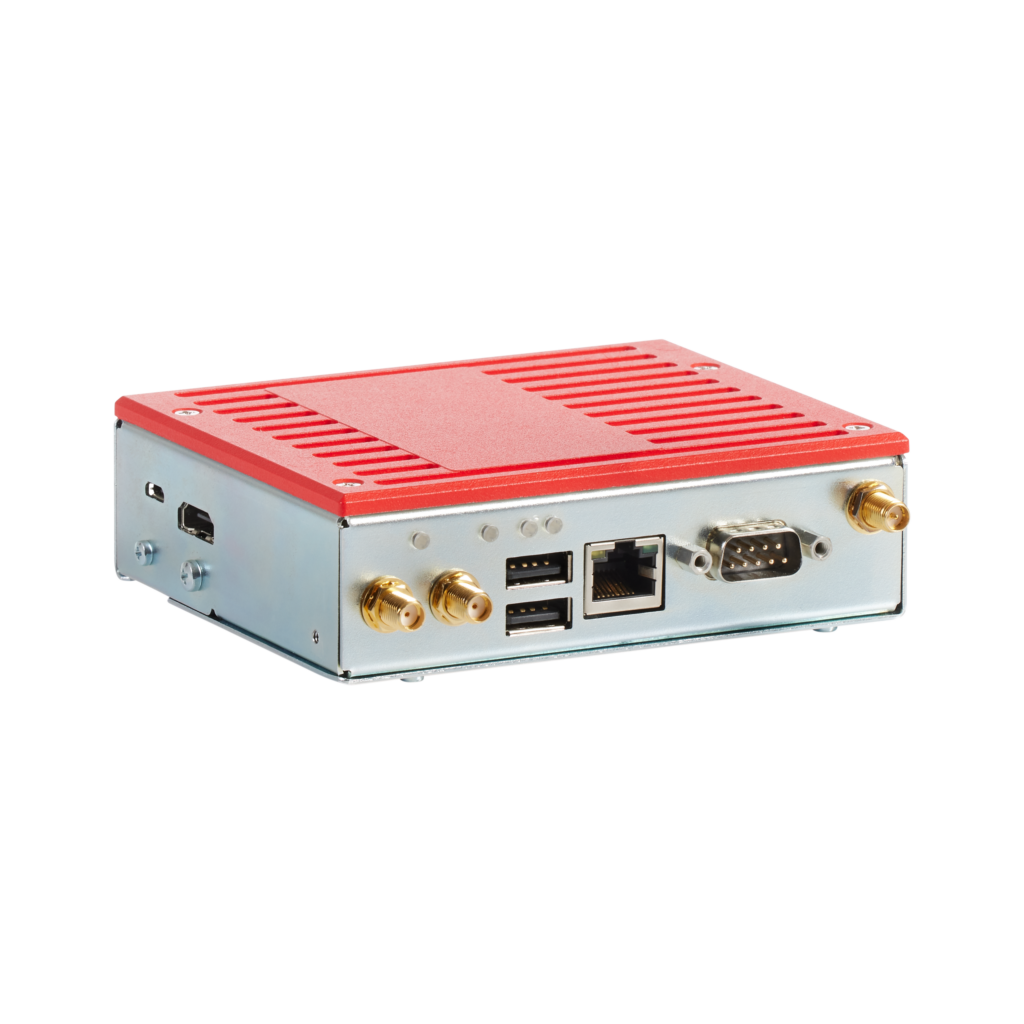
Janz Tec emPC-A/RPI3(+)
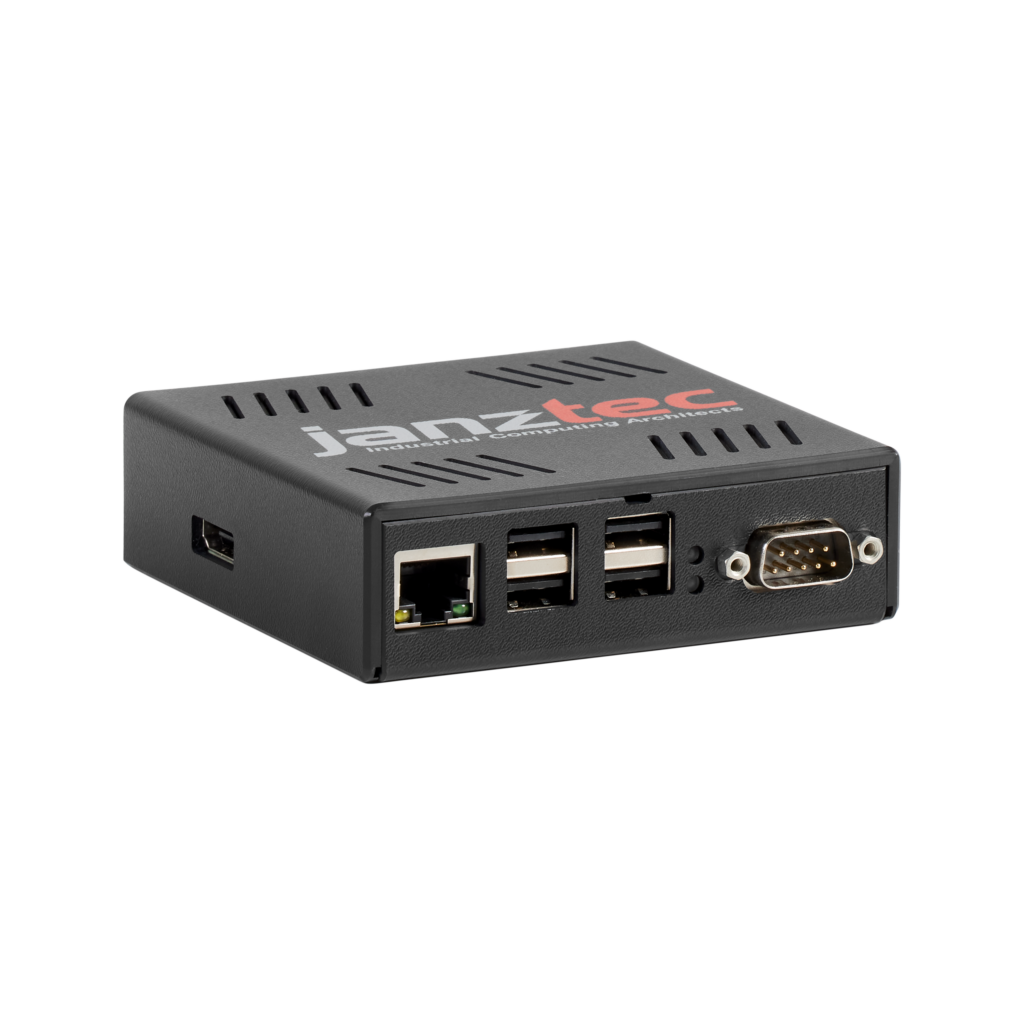
Janz Tec emPC-A/iMX6
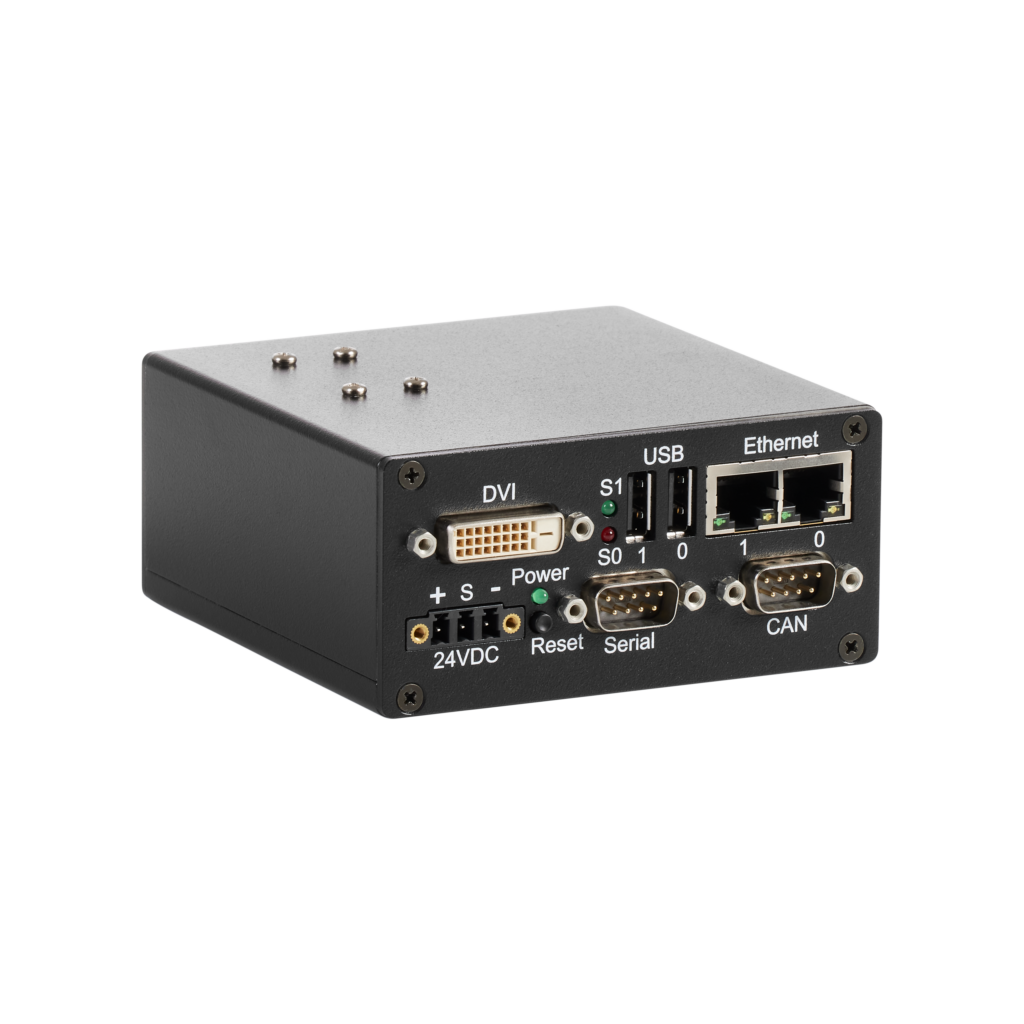
Product Specifications
- i.MX6 embedded Computing Unit
- 800 MHz Quadcore
- 2 GByte System Memory
- NVRAM
- CFAST Socket
- 2x Gigabit/s Ethernet
- Extended Temperatures from -40°C to 75°C
- Interfaces (RS232, RS485, CAN, CAN-FD Digital I/O, Anaolg I/O, …) configurable ex works
- Also available as Panel with 6” to 21” Touch Display
Kontron AL Pi-Tron CM4
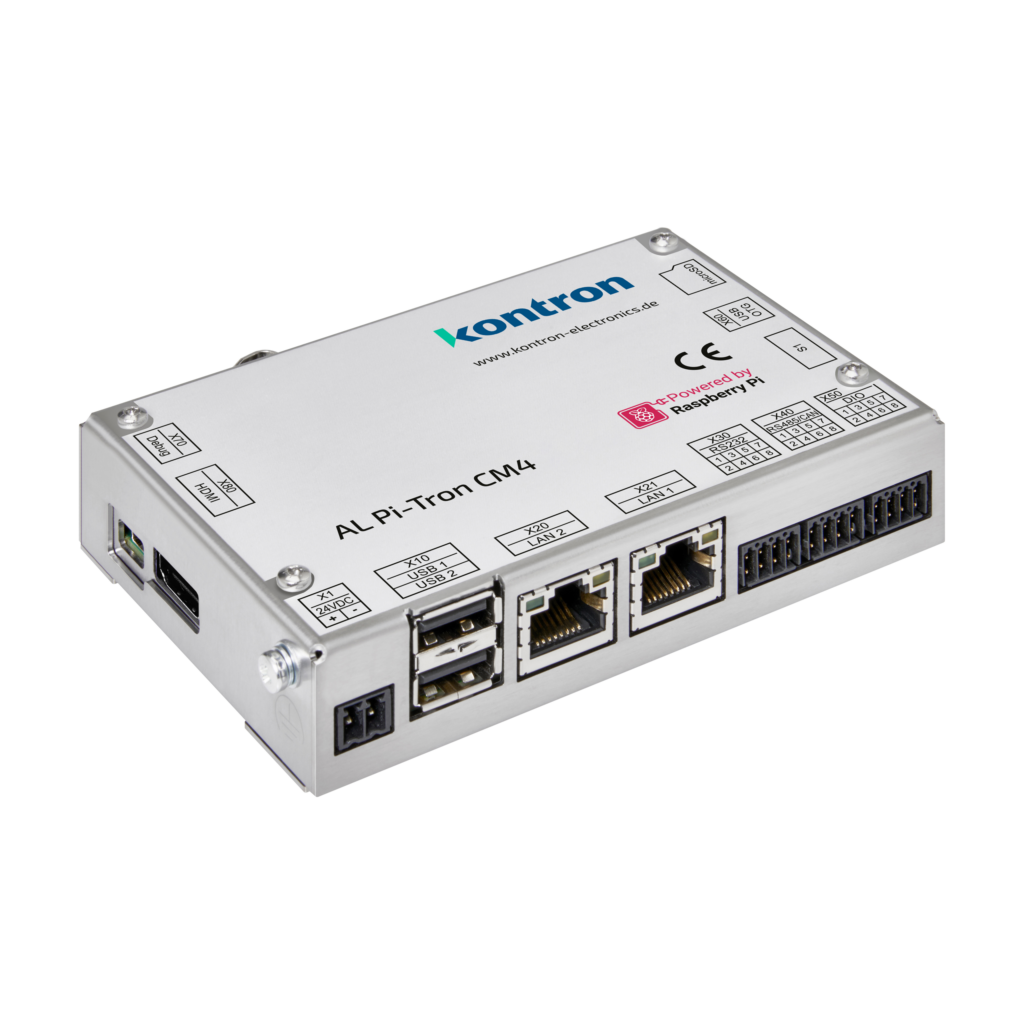
Kontron AL Pi-Tron CM3+
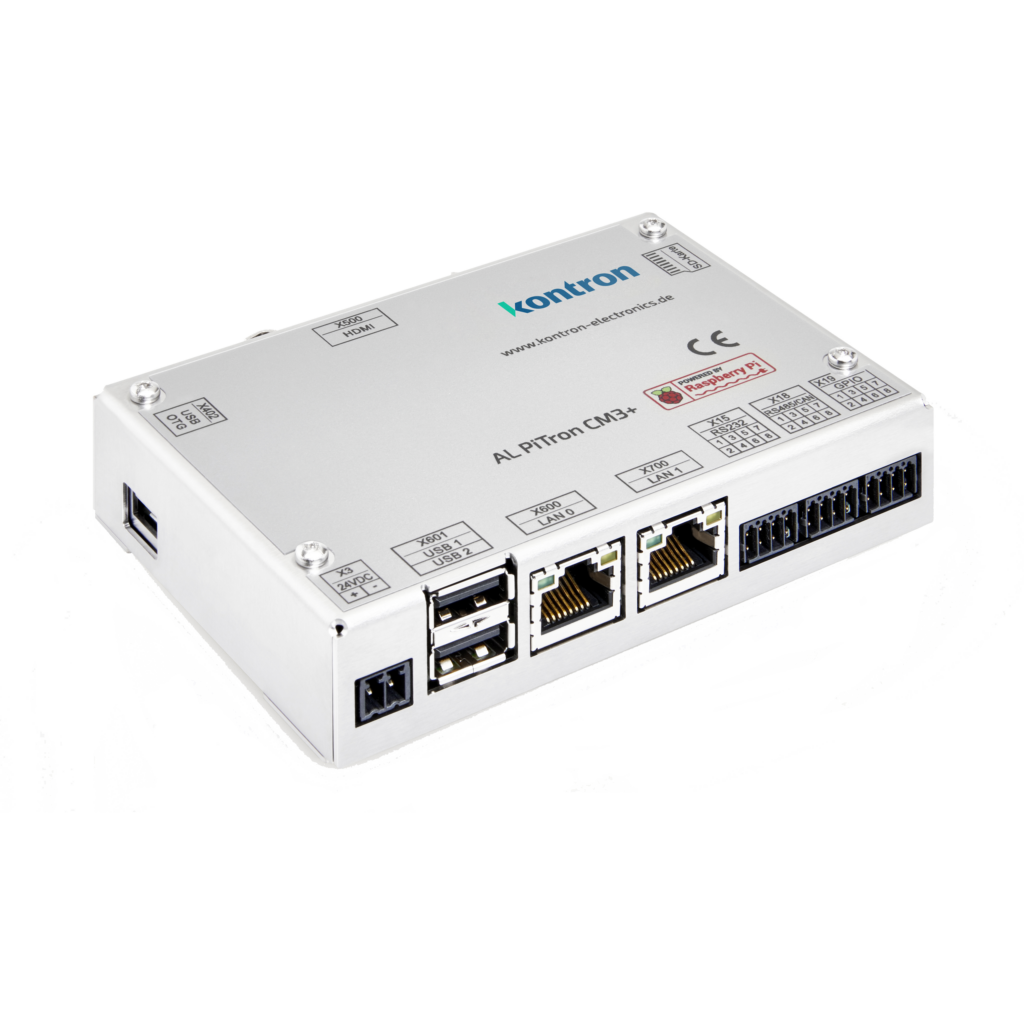
Kontron AL i.MX8M Mini
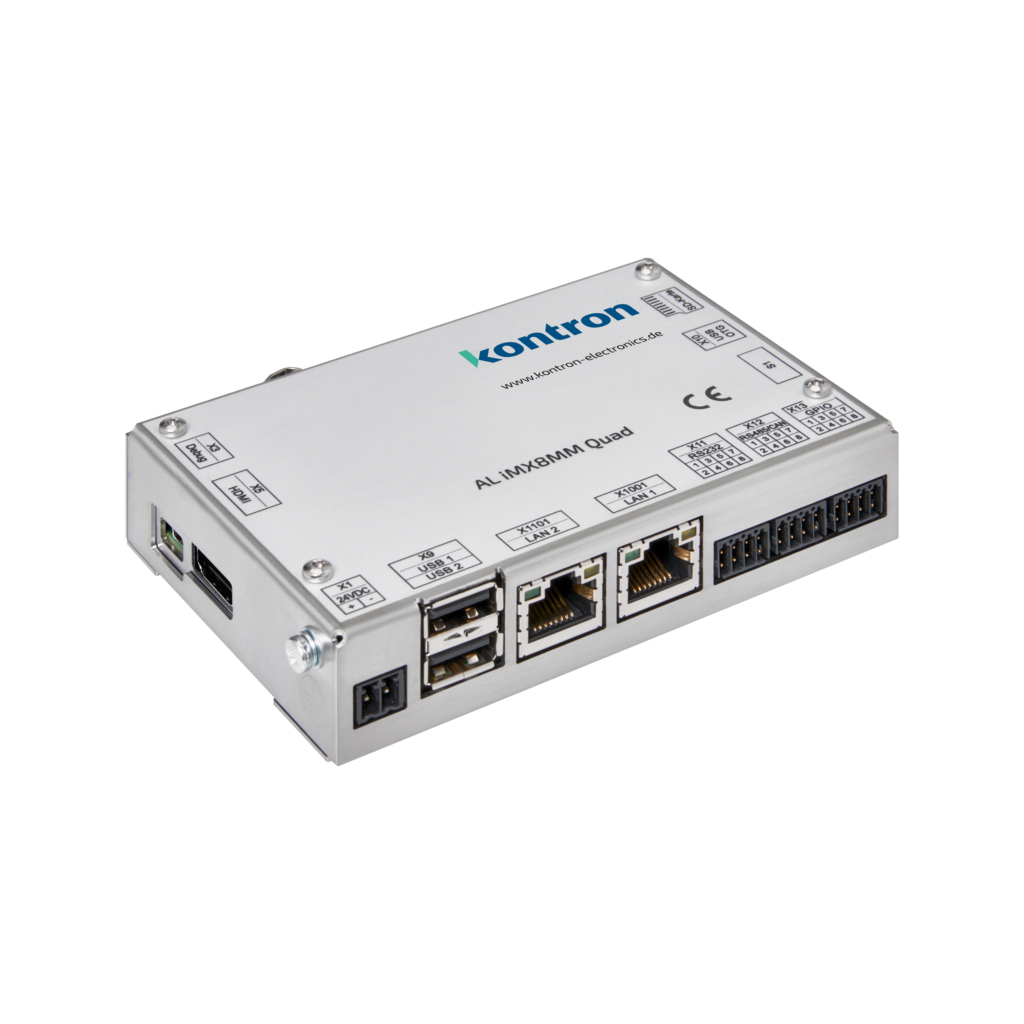
Embedded PCs
Our Scalable Embedded PCs consist of the emPC-X and emPC-CX+ series, which have a long history of success. The emPC-X is a compact x86 computer that boasts many interfaces and high performance despite its comparatively small size. The emPC-CX+ is known for its high degree of scalability. A range of expansion cards ensures that you can tailor the system entirely to your application. The choice of software is also up to you – our team will try to meet all your requirements. All embedded PCs are also available as panel PCs.
Here you can find a selection of possible basic systems and configurations.
Our team of experts will gladly assist you with individual requirements at any time.
Janz Tec emPC-CX+
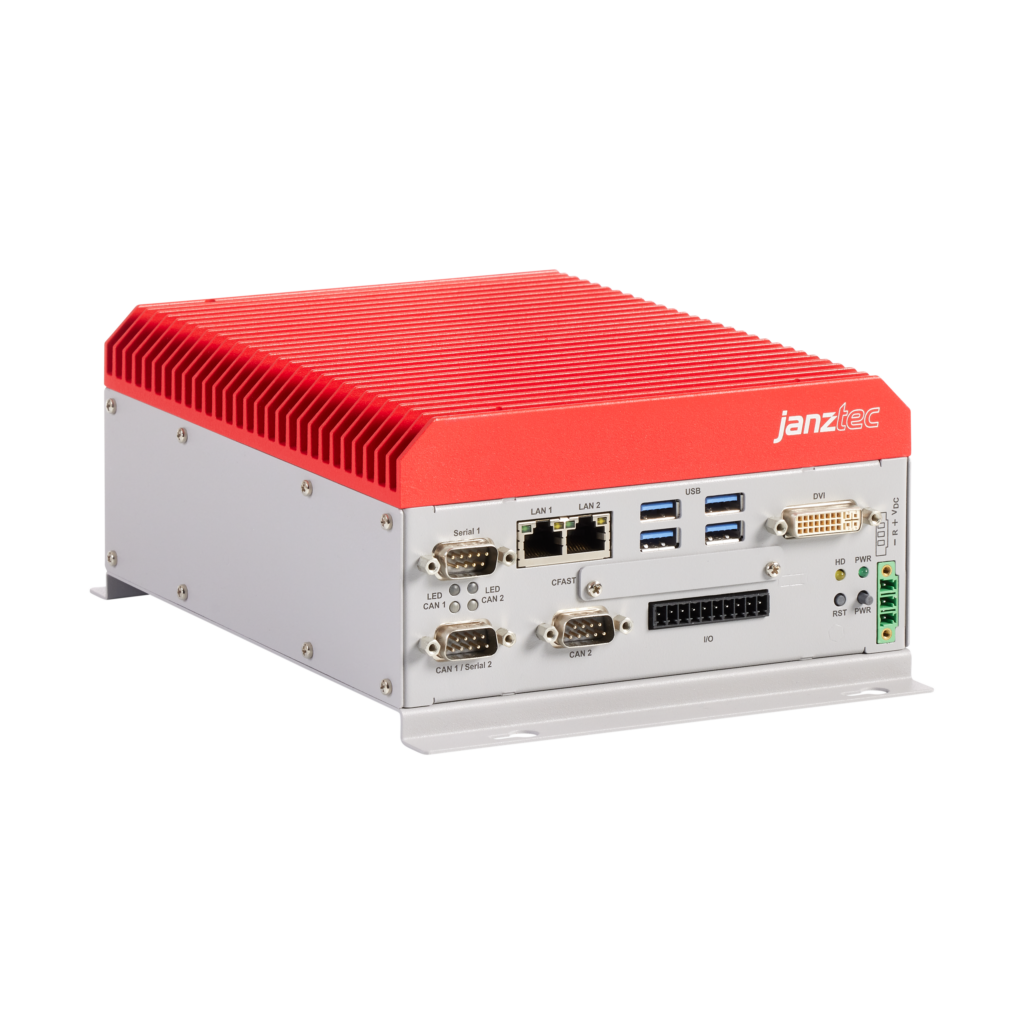
Janz Tec emPC-X
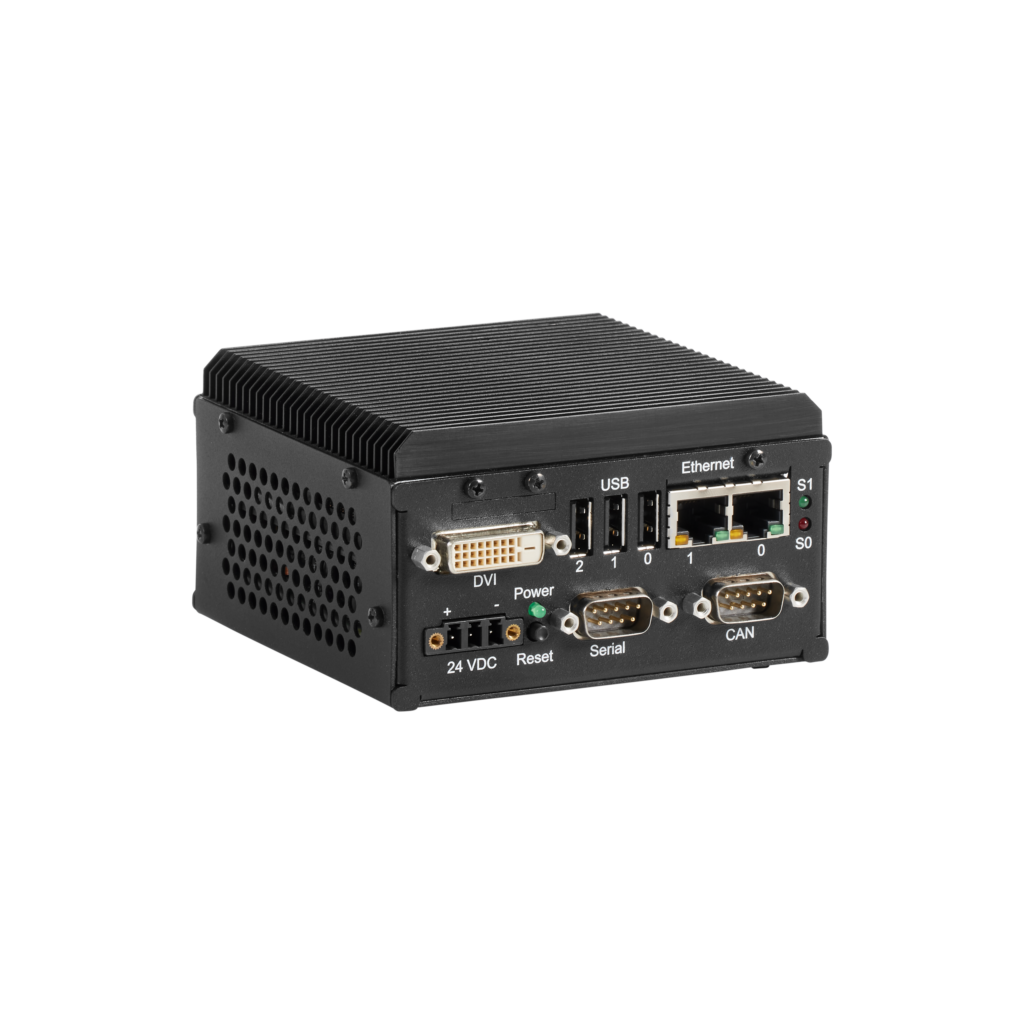
Compact Industrial PCs
Our Compact IPCs offer intelligent solutions for IoT edge applications as well as powerful and flexible box PCs for industrial control and data acquisition. A wide range of interfaces and scalable performance classes ensure that the systems can meet numerous requirements.
Here you can find a selection of possible basic systems and configurations.
Our team of experts will gladly assist you with individual requirements at any time.
Janz Tec FALCON active
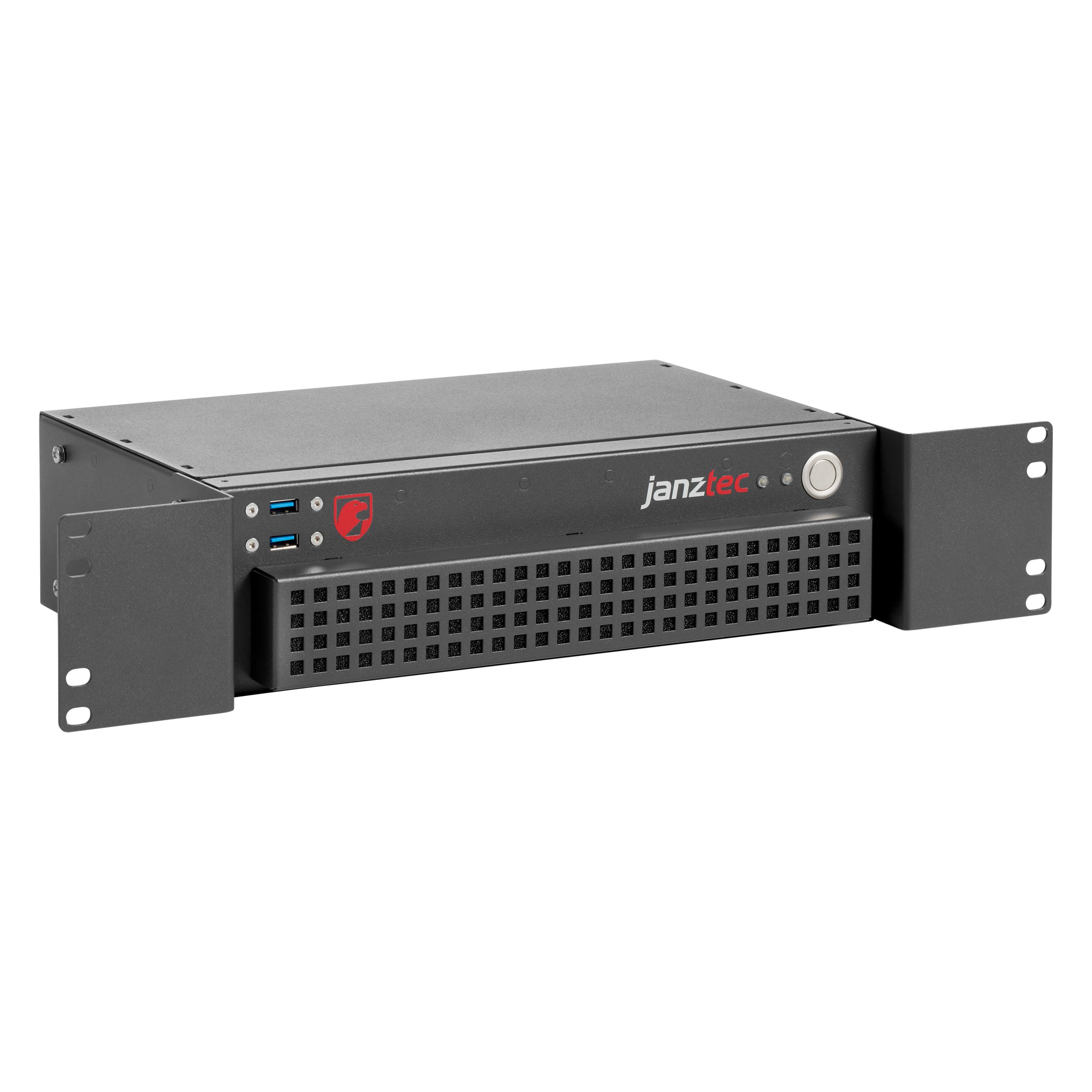
Advantech UNO-148
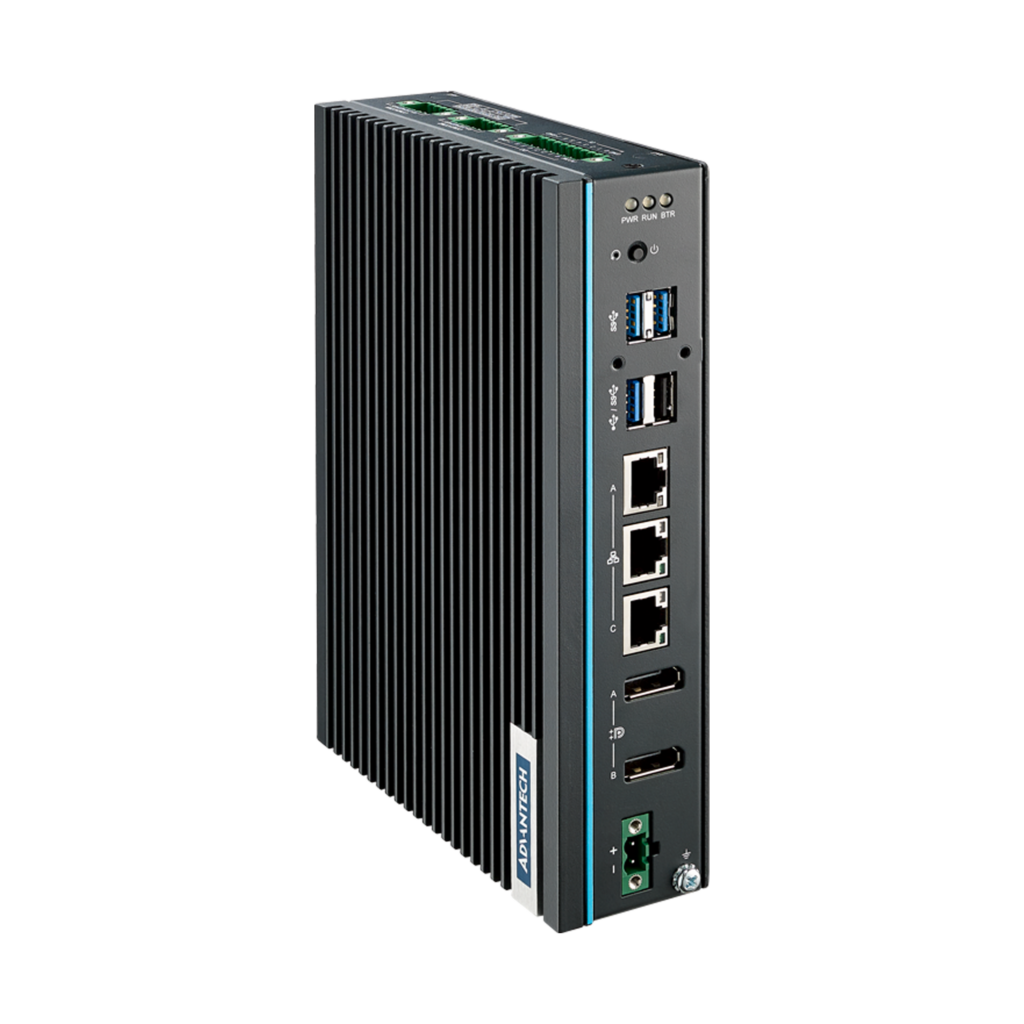
Kontron KBox A-250
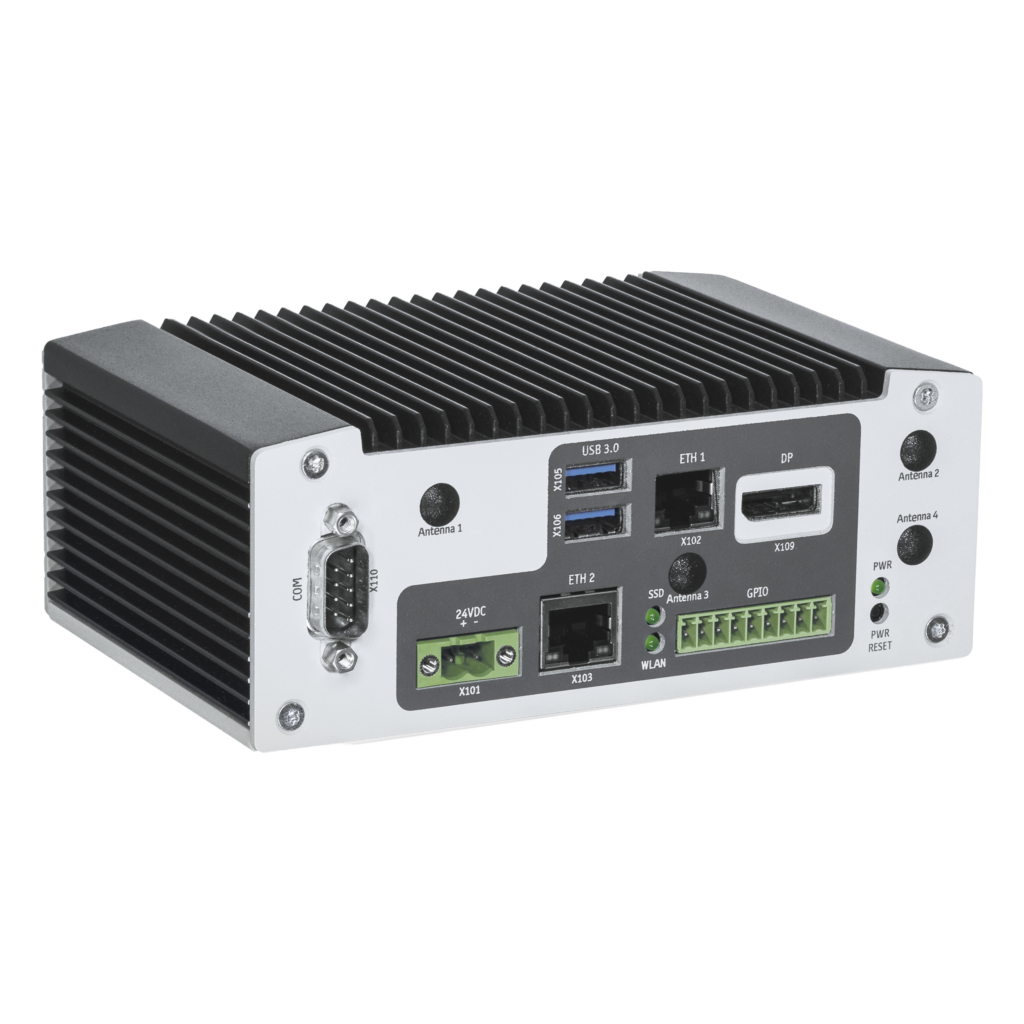
Kontron KBox A-151
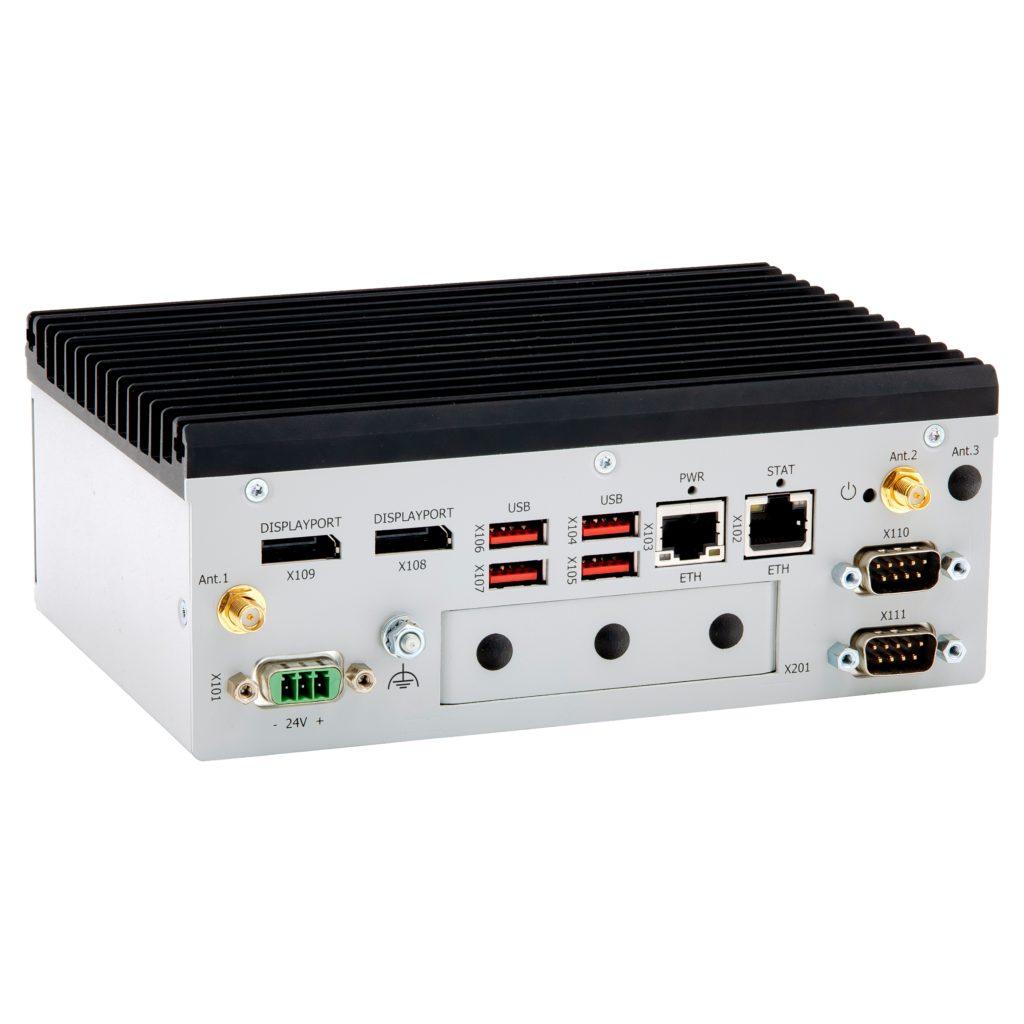
Advantech UNO-127

Advantech UNO-137

Advantech IPC-220 & IPC-240
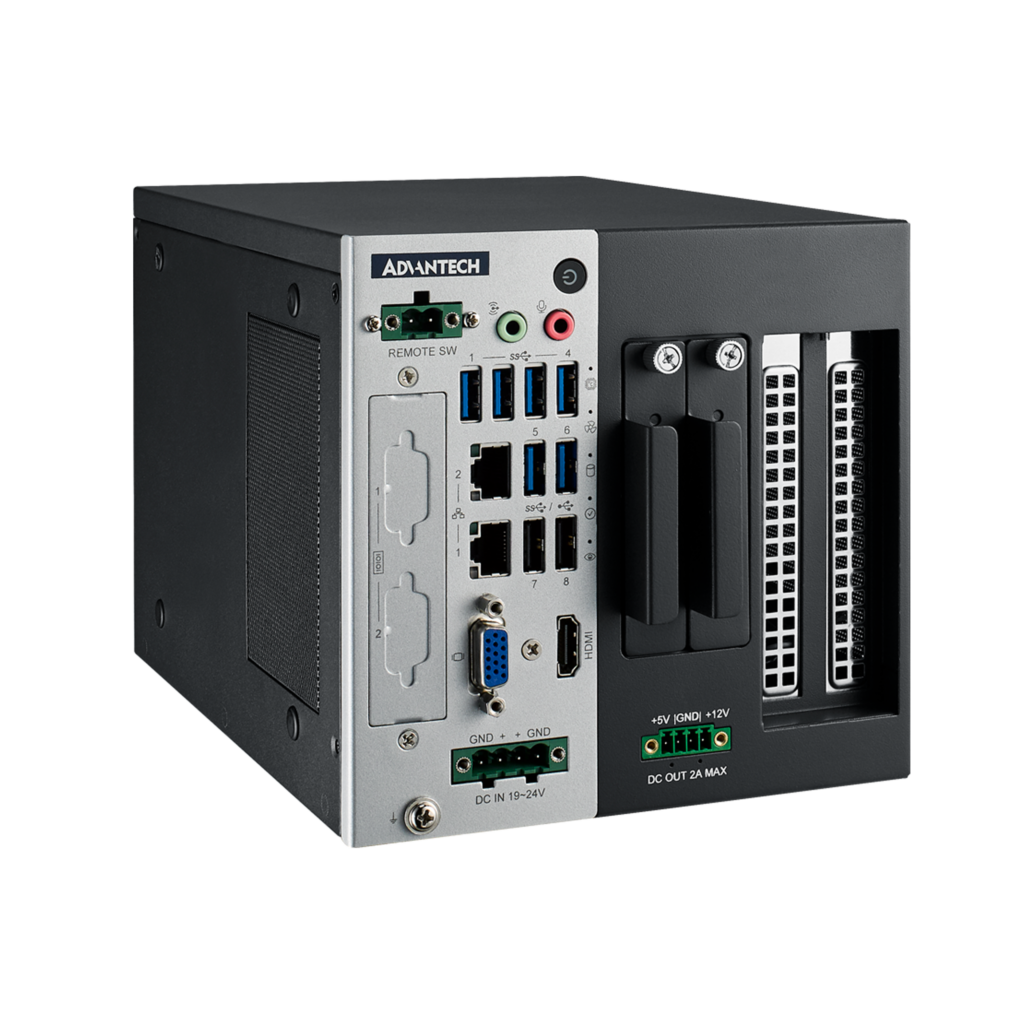
Modular Industrial PCs
Thanks to their modular design, the IPCs are extensively expandable and scalable to meet various industrial requirements.
Here you can find a selection of possible basic systems and configurations.
Our team of experts will gladly assist you with individual requirements at any time.
Advantech MIC-770
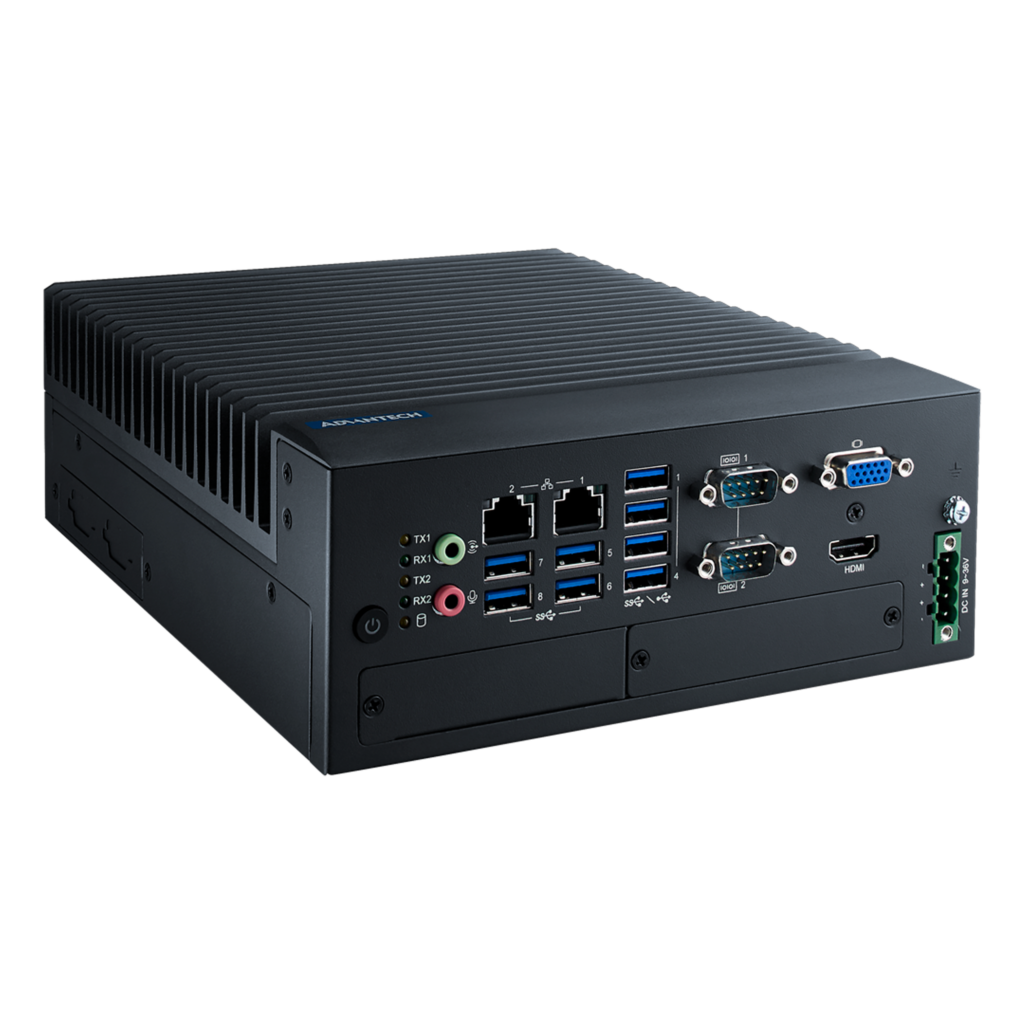
Advantech MIC-770 i-Module

Rugged PCs
Our fanless rugged PCs are designed for harsh environments and extreme temperatures. Thanks to their IP protection ratings, they are both dust and water protected and suitable for use in demanding applications, e.g. in vehicles, on trains or outdoors.
Here you can find a selection of possible basic systems and configurations.
Our team of experts will gladly assist you with individual requirements at any time.
Kontron KBox R-101
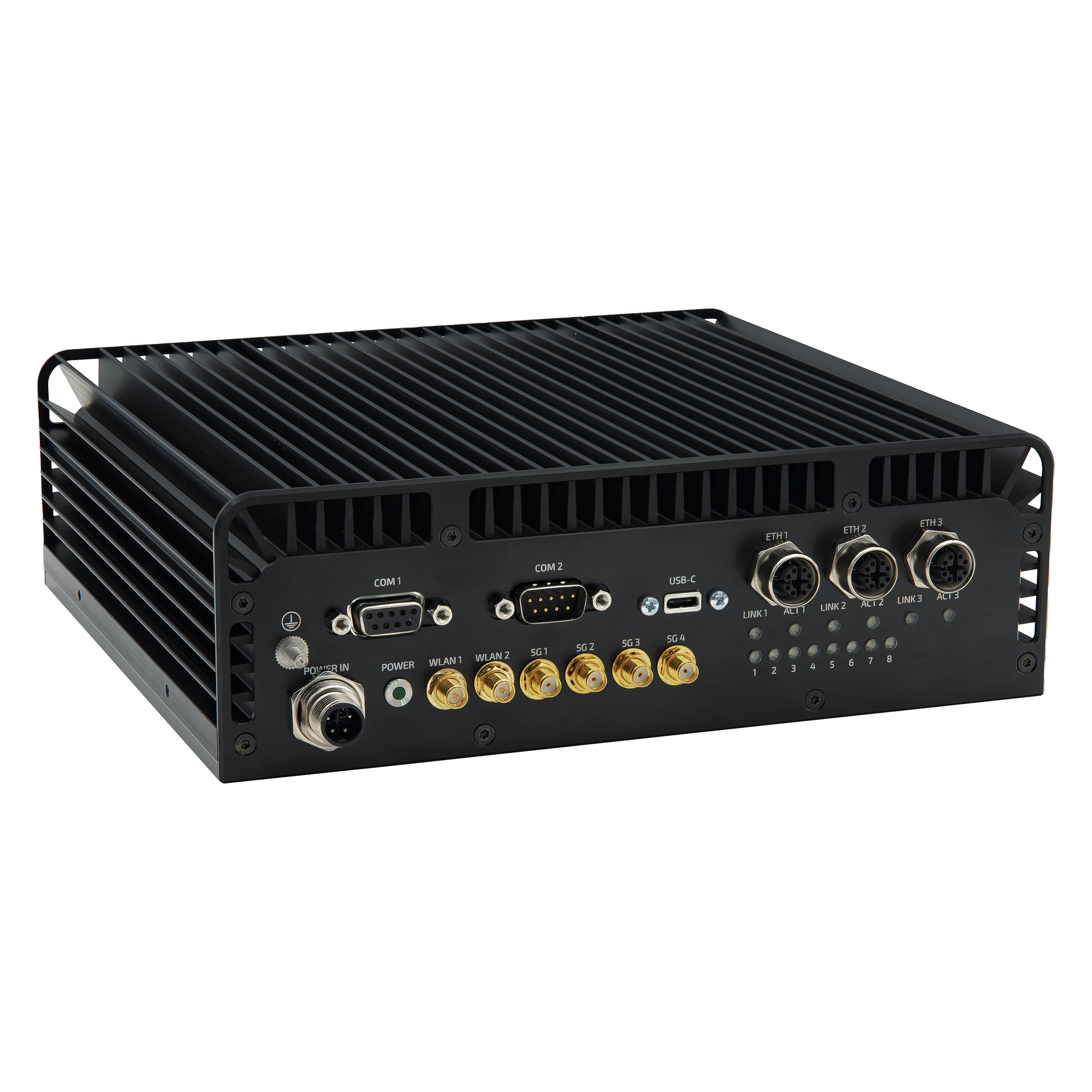
Advantech MIC-715
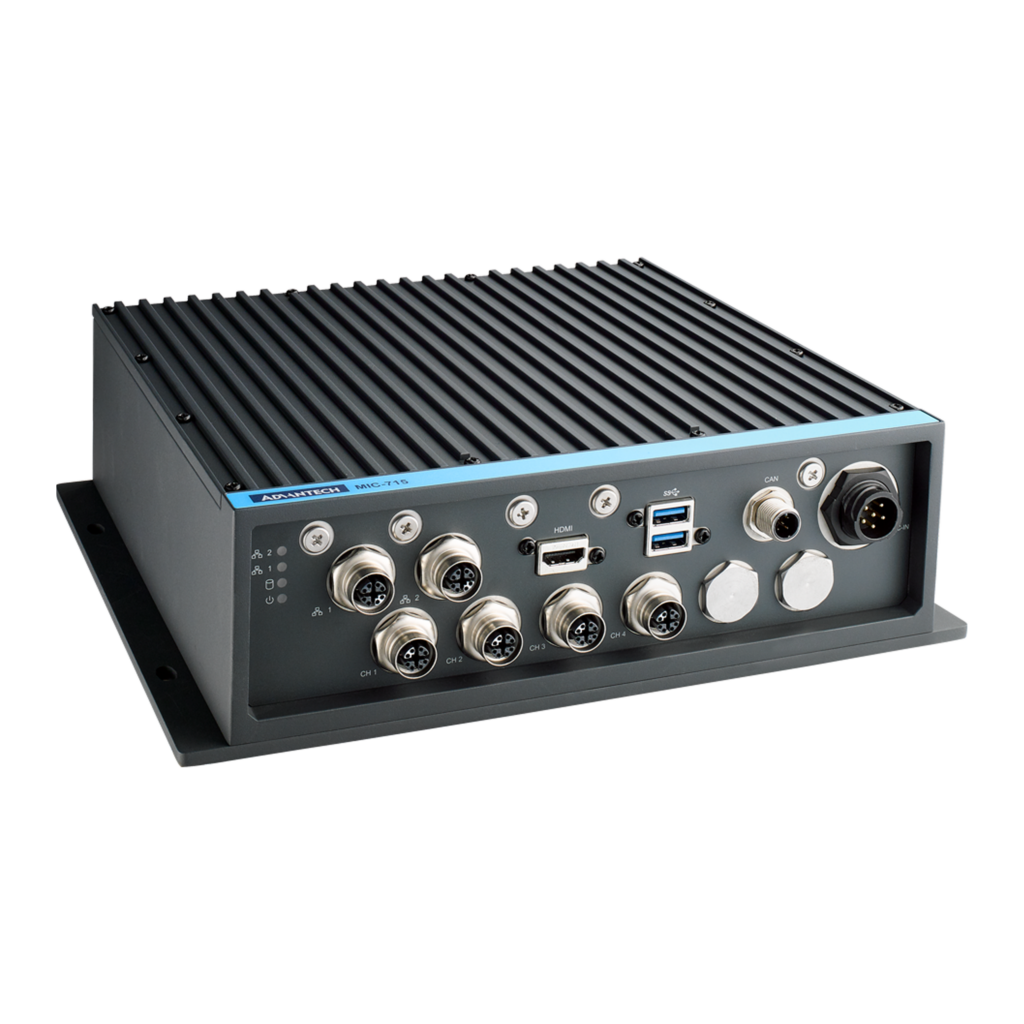
Advantech TS-207
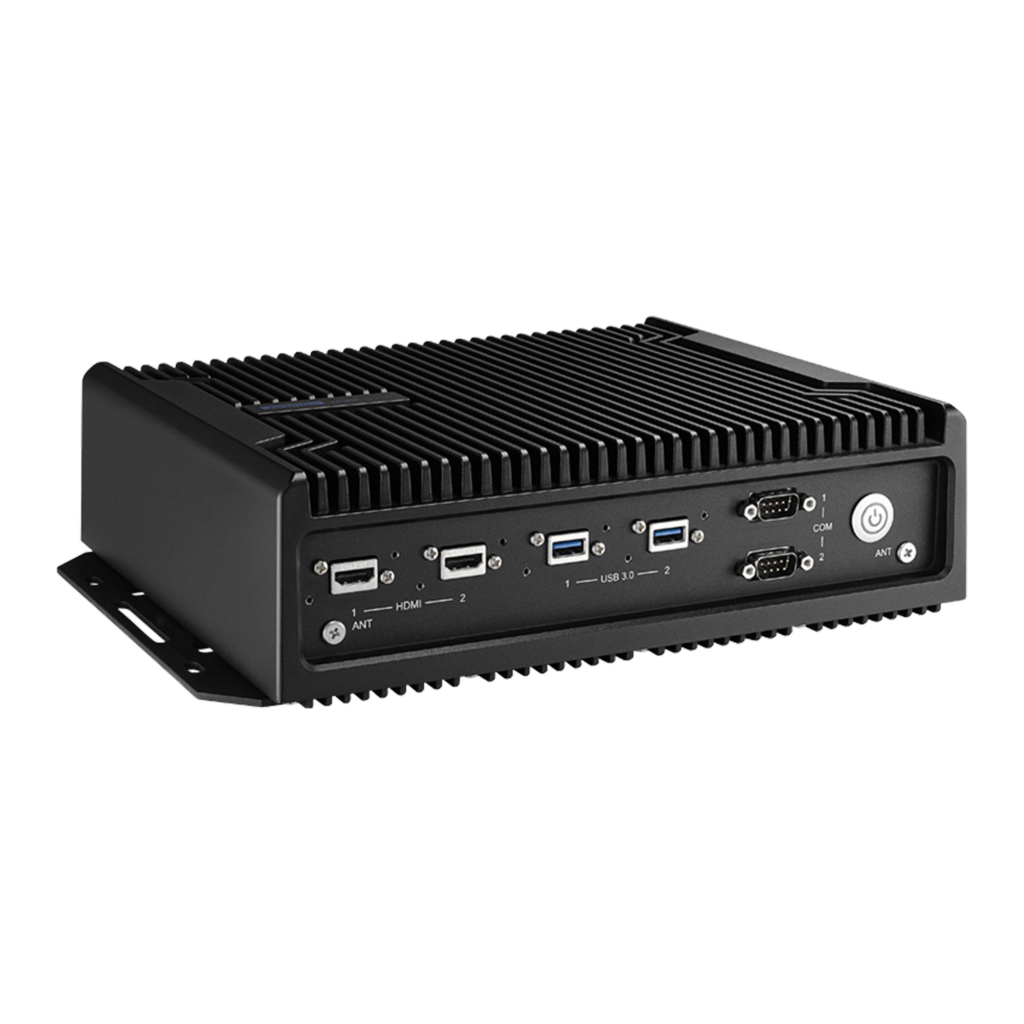
Rackmount Industrial PCs
Our 19″ rackmount IPCs are available in 1U, 2U and 4U with different mainboard variants or as an SBC/backplane solution. They offer a variety of expansion slots for excellent scalability.
Here you can find a selection of possible basic systems and configurations.
Our team of experts will gladly assist you with individual requirements at any time.
Janz Tec ATLANTIS 4U SBC
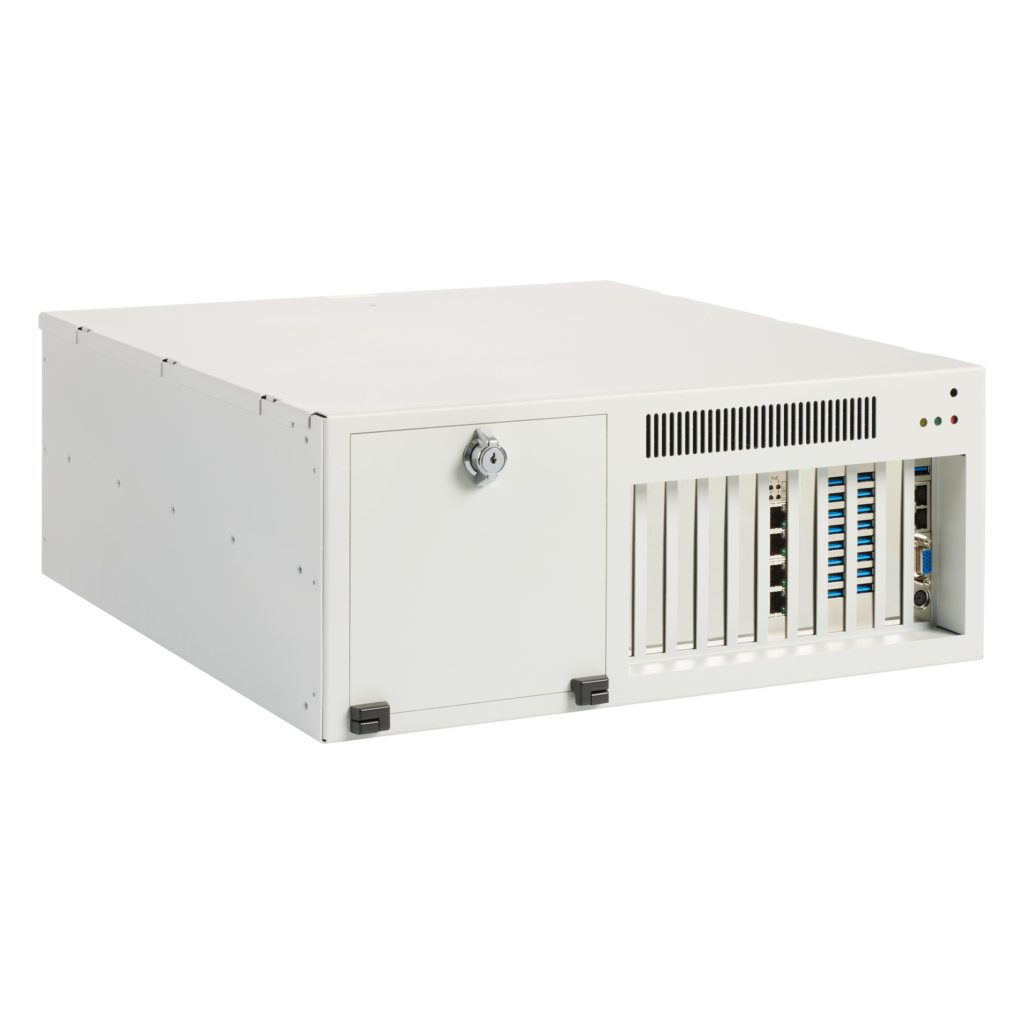
Kontron KISS 1U
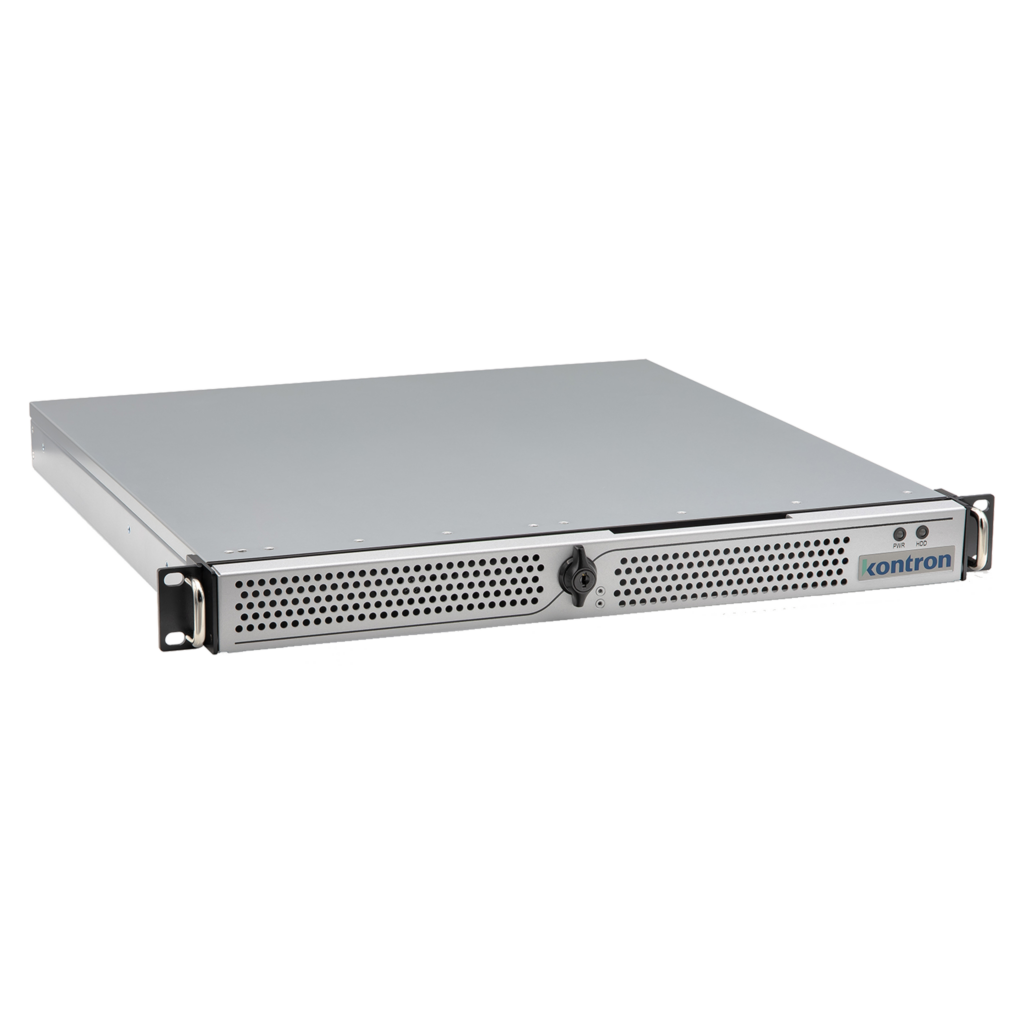
Kontron KISS 2U
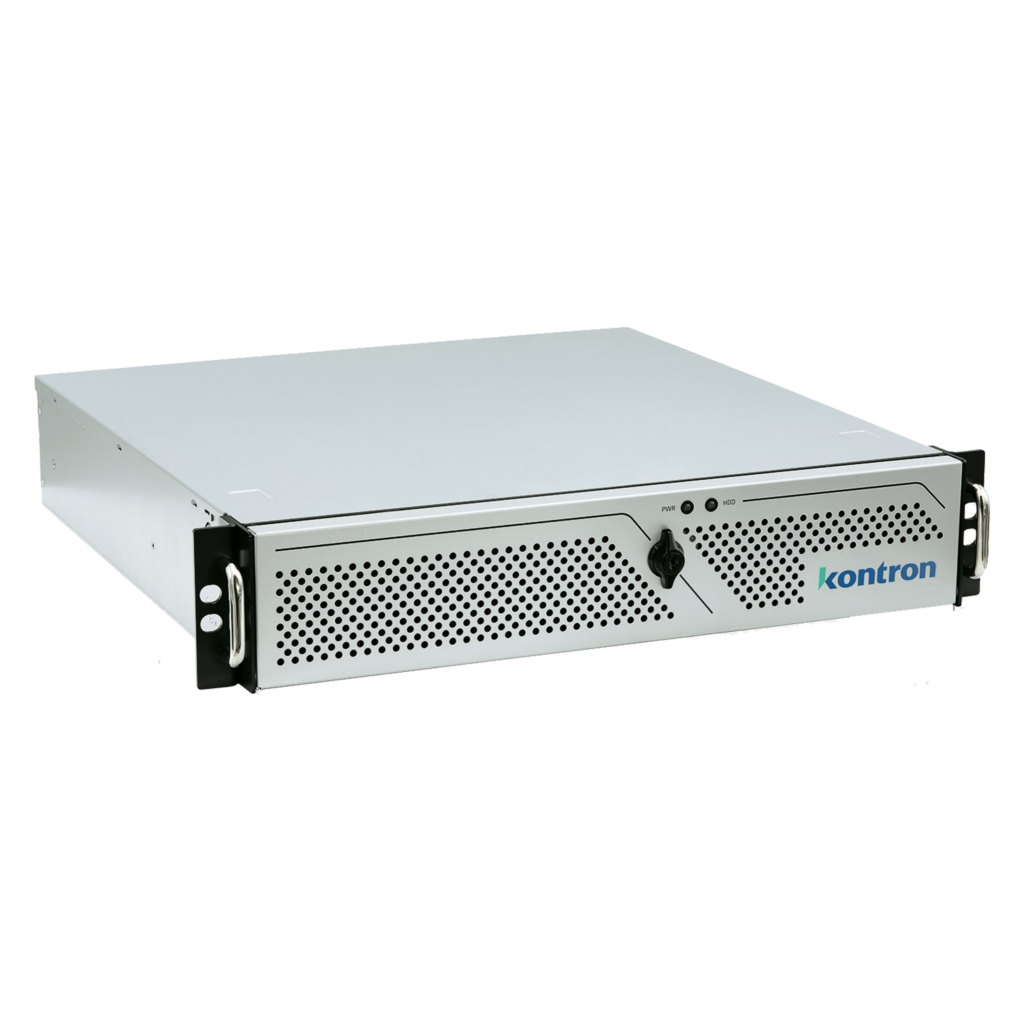
Kontron KISS 4U
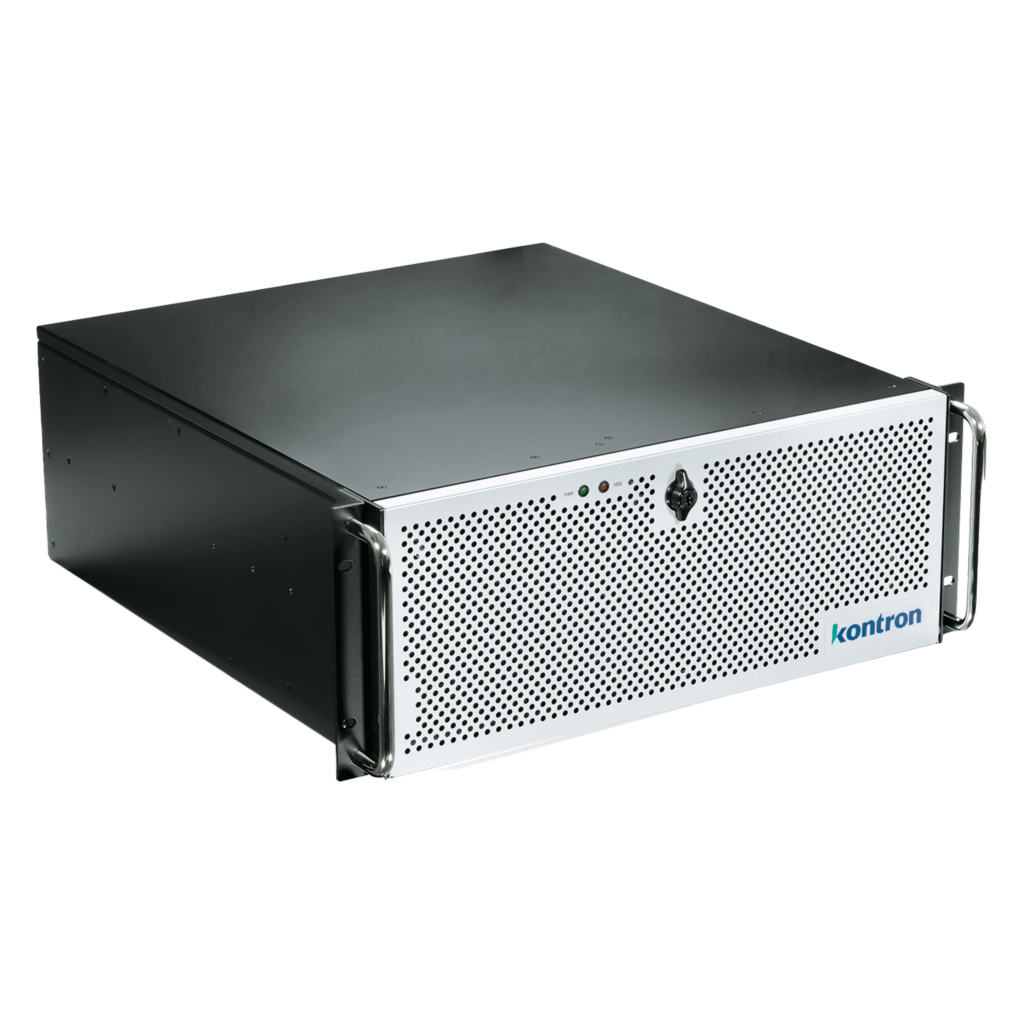
Advantech 4U ACP-4340
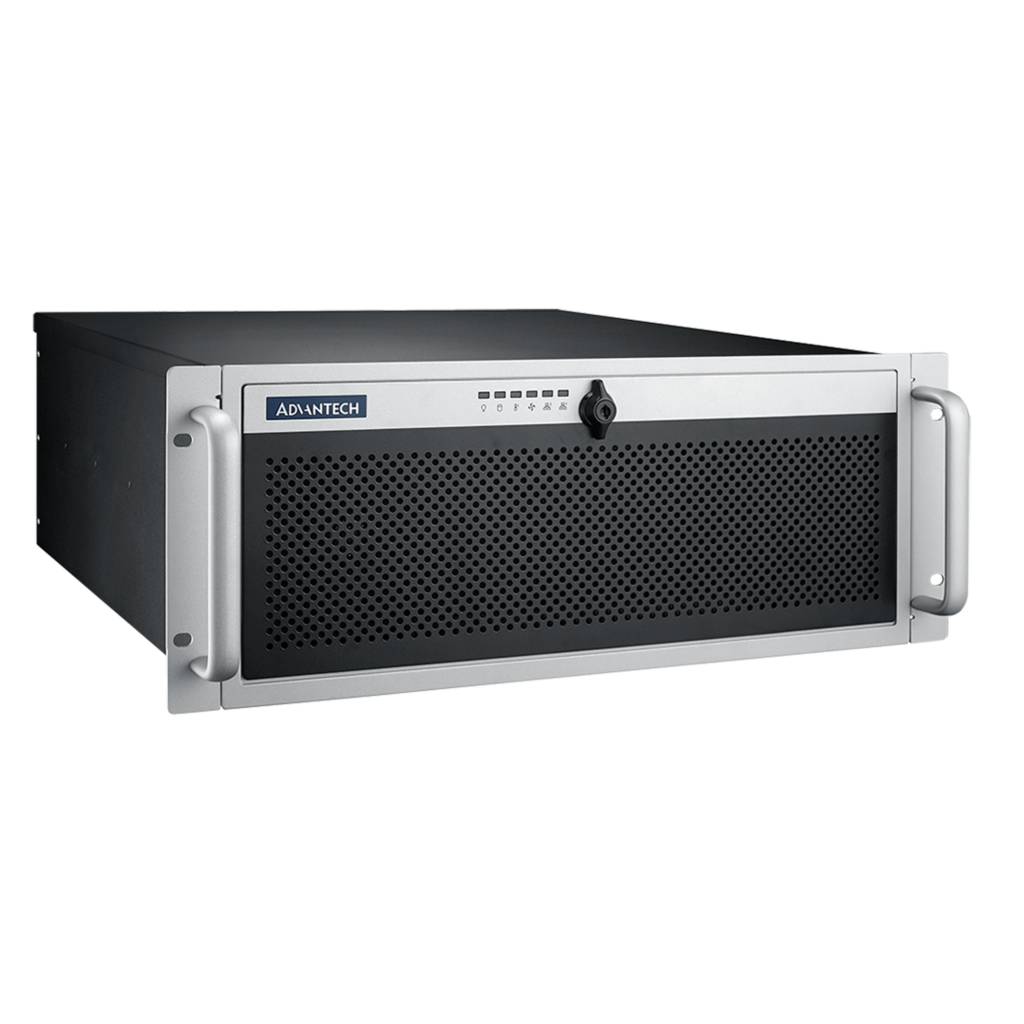
Advantech 4U ACP-4020
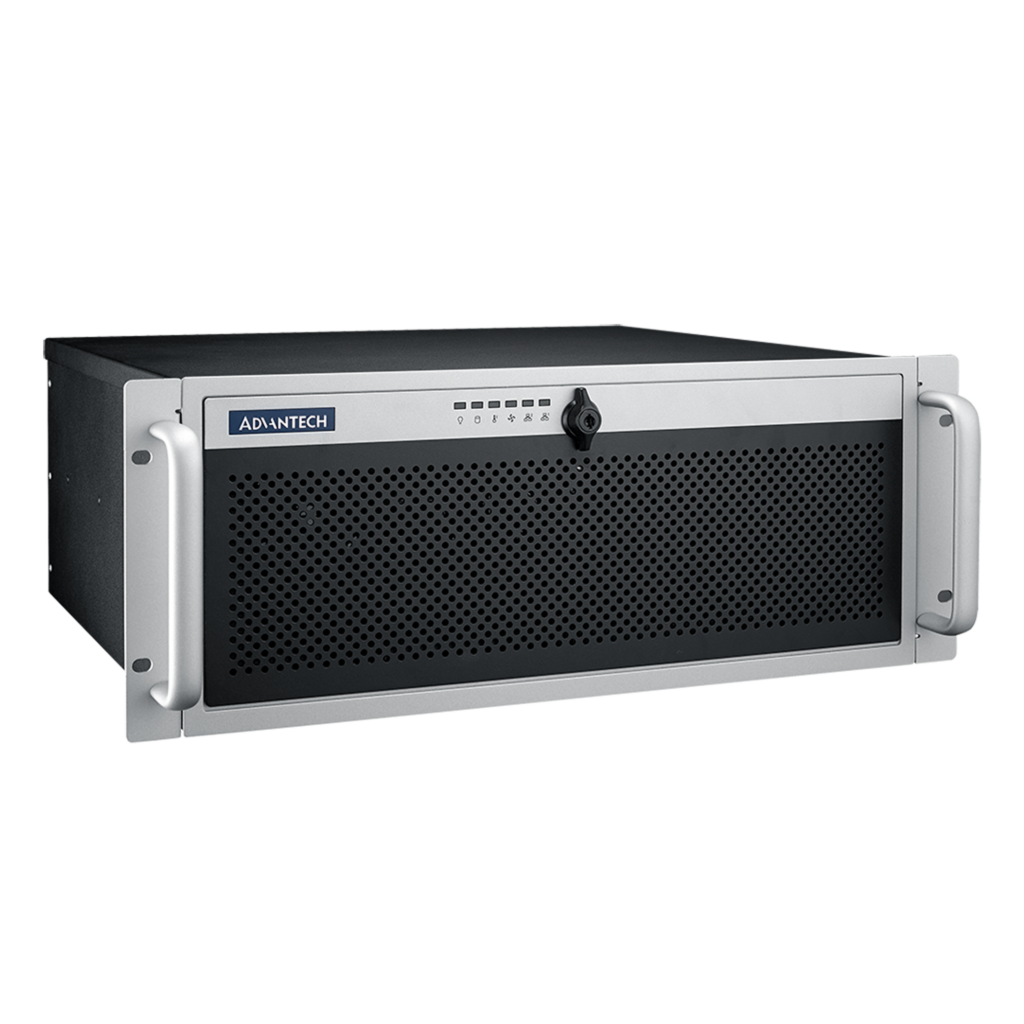
Advantech 2U ACP-2020
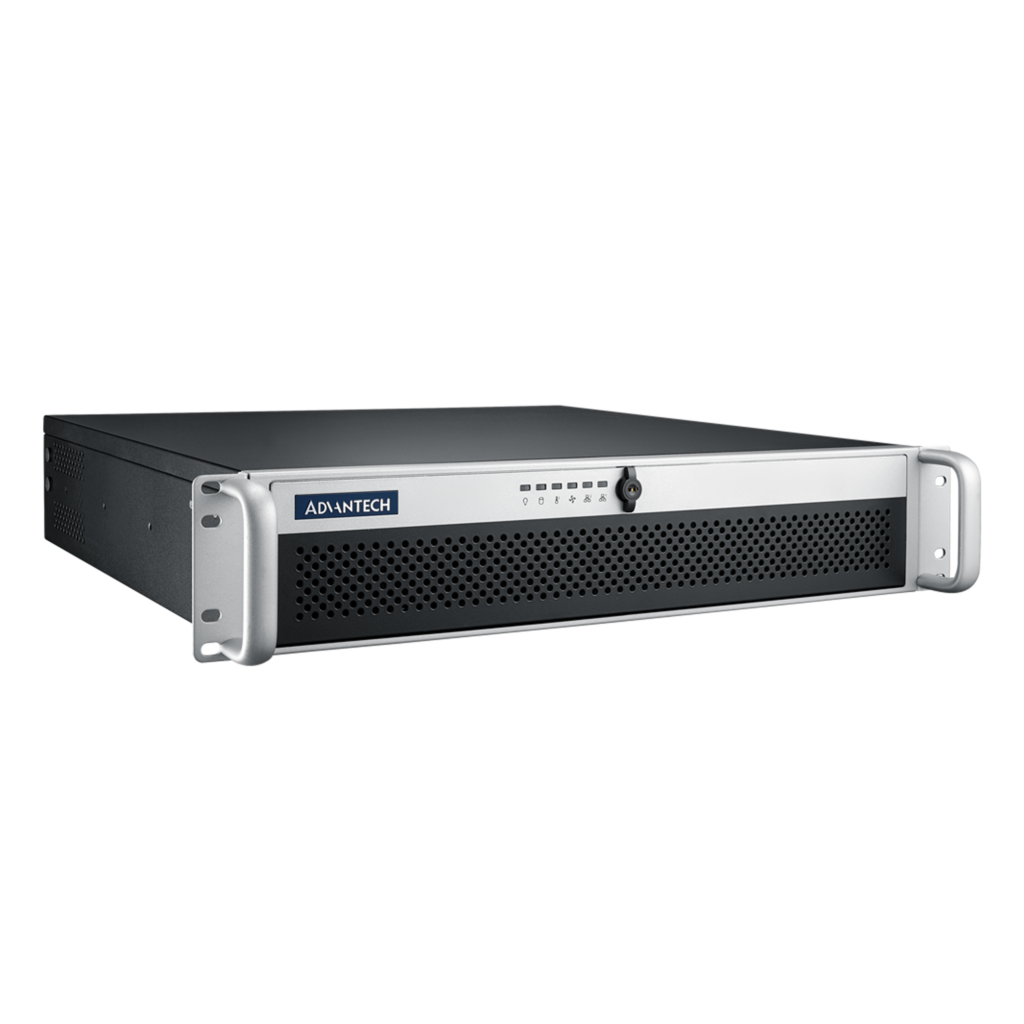
Advantech 4U IPC-631
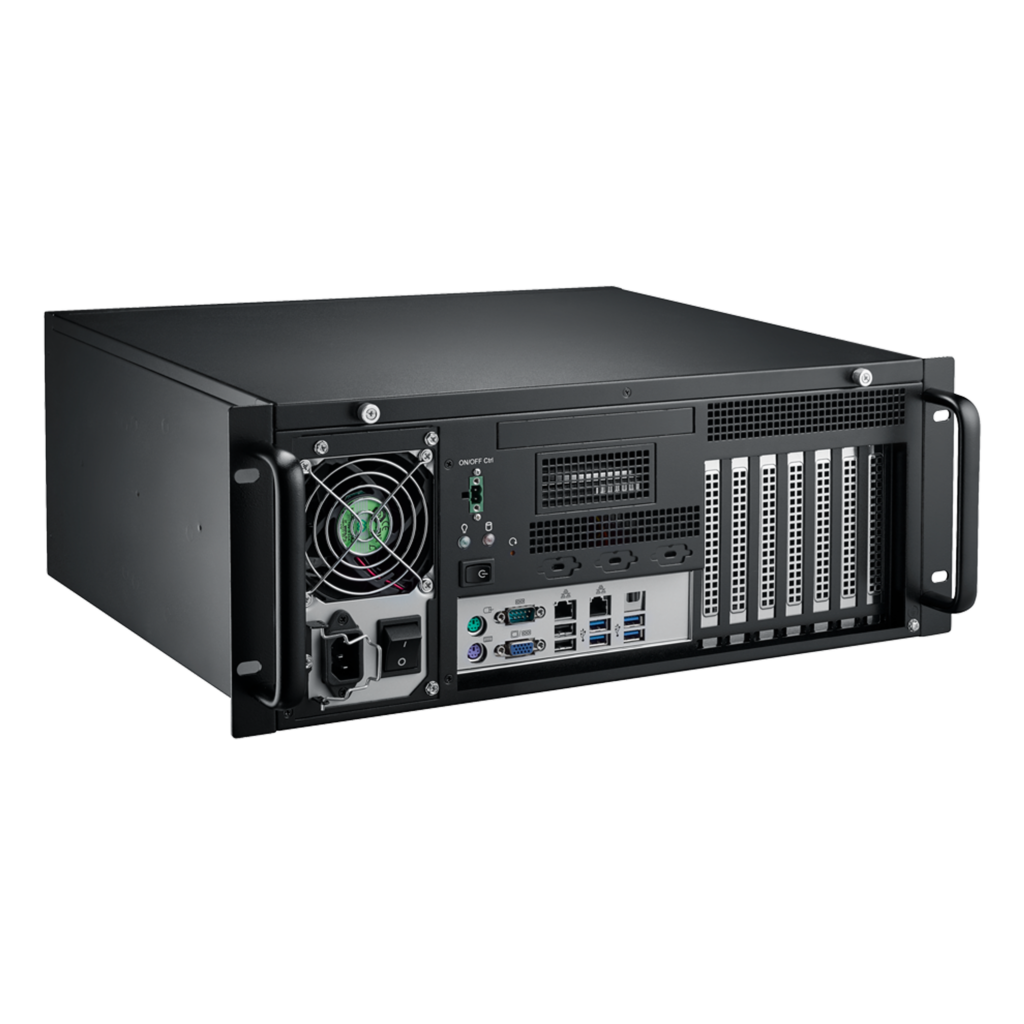
Wallmount & Desktop Industrial PCs
Our wallmount and desktop IPCs are available with different mainboard variants or as an SBC/backplane solution. They offer a variety of form factors, interfaces and scalable performance for diverse applications.
Here you can find a selection of possible basic systems and configurations.
Our team of experts will gladly assist you with individual requirements at any time.
Janz Tec ENDEAVOUR SBC
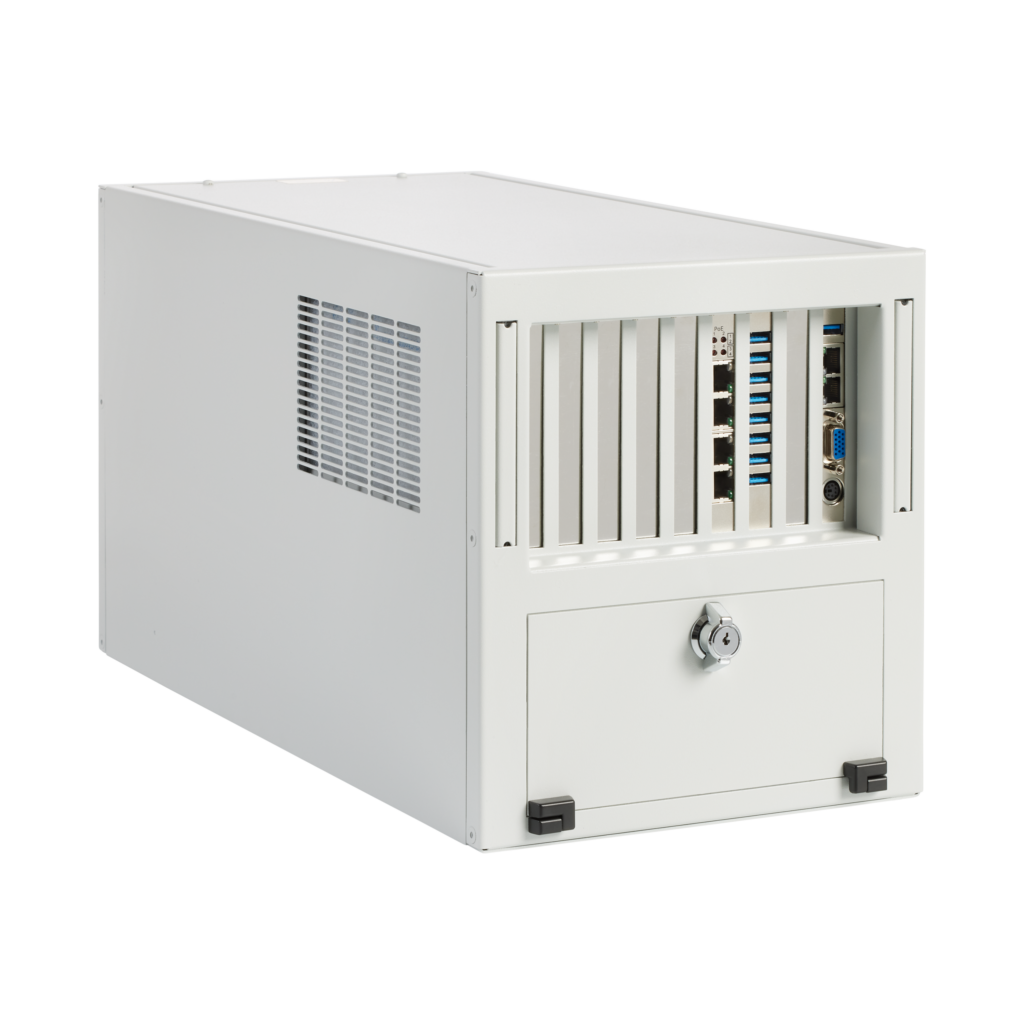
Advantech IPC-320

Advantech EPC-B5000
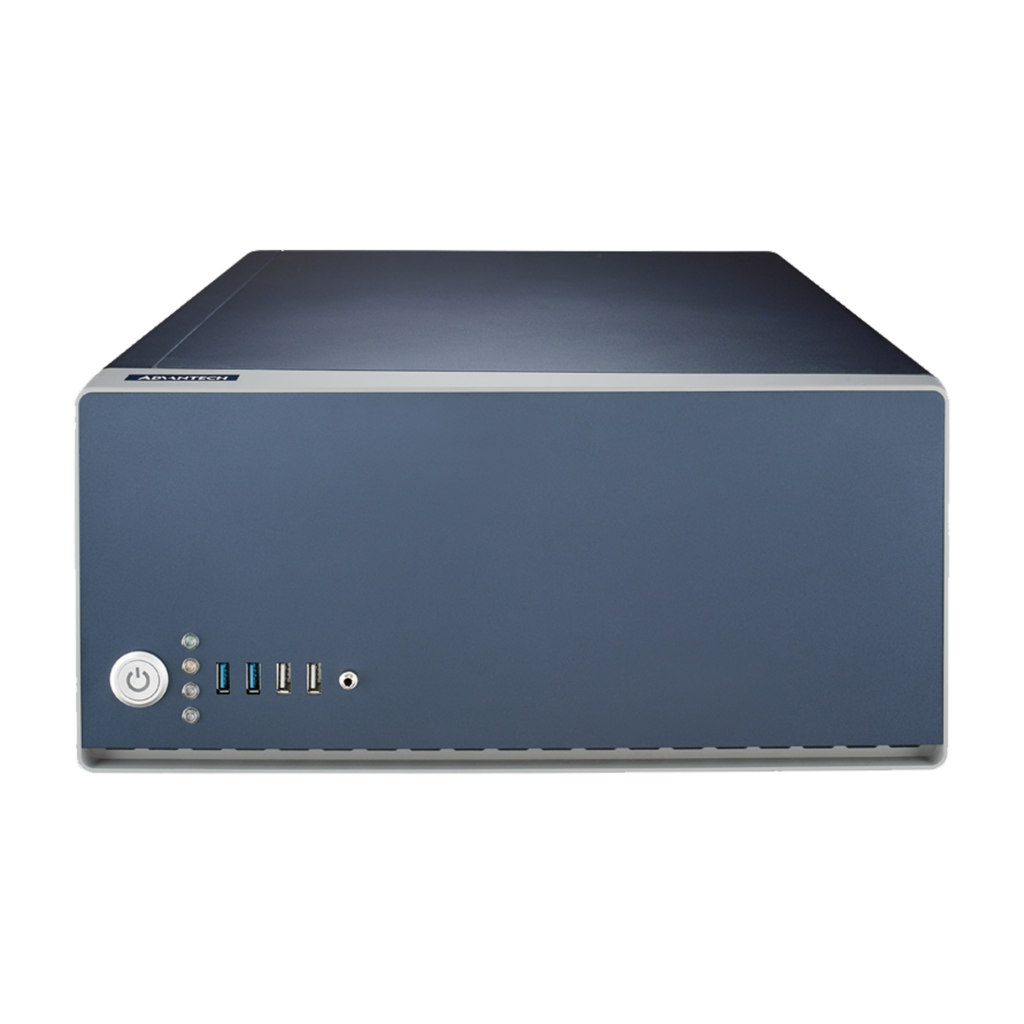
Kontron KWS 3000
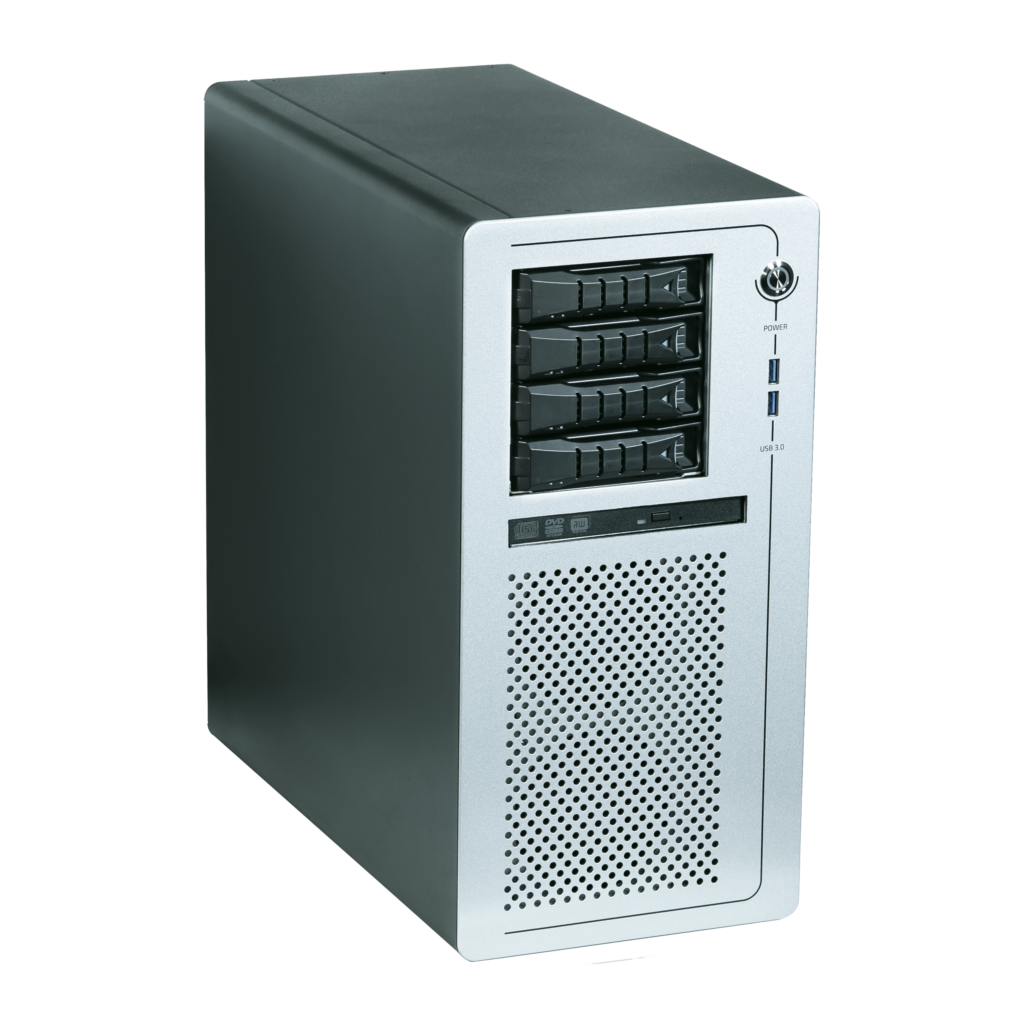
Kontron KBox B-201
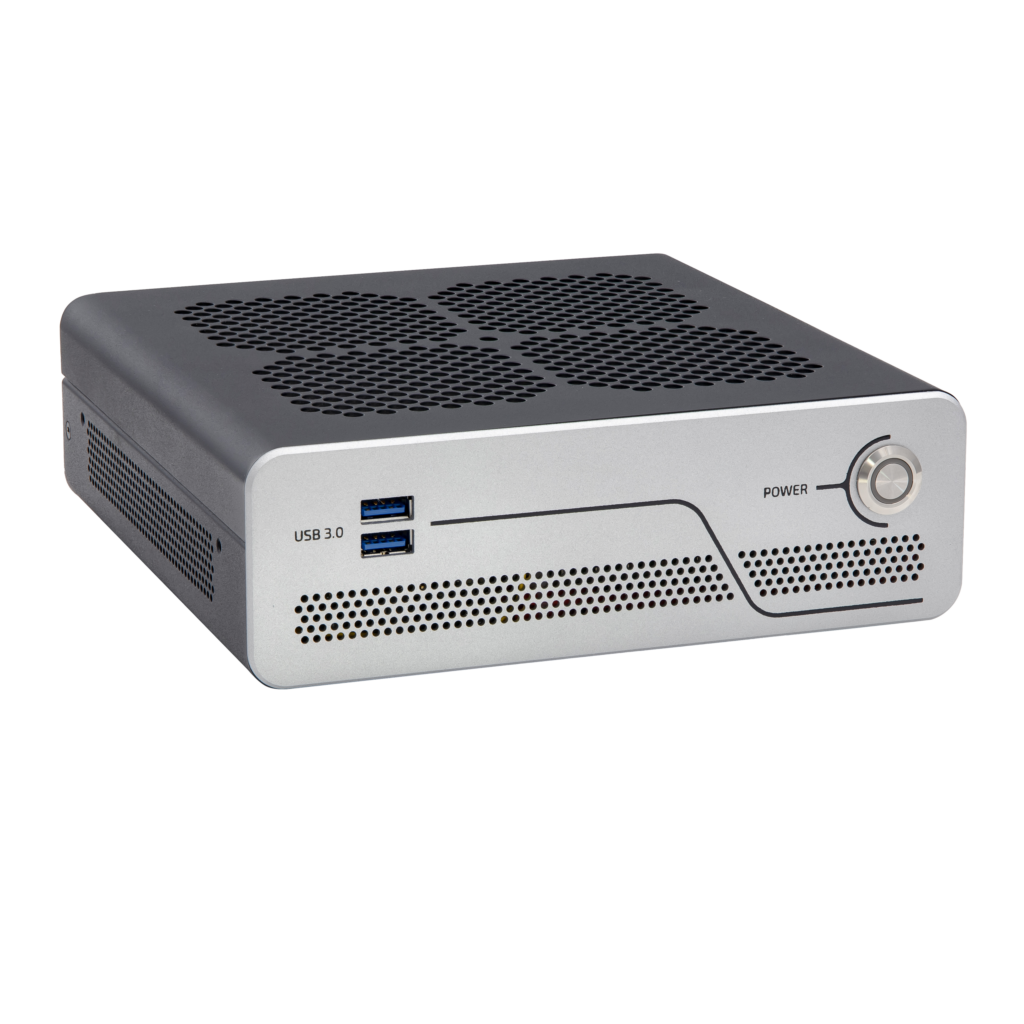
Advantech IPC-242
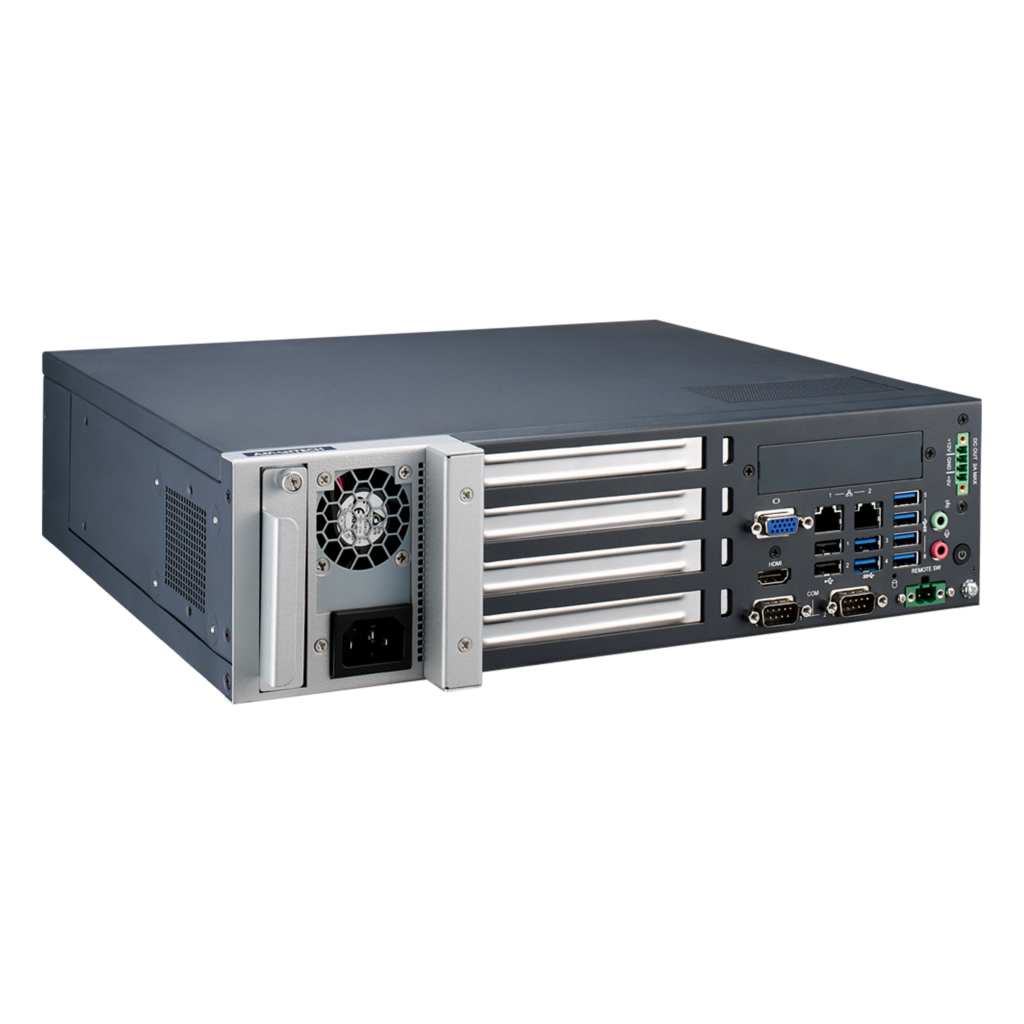
Industrial GPU & AI Solutions
These IPCs are suitable for edge AI inferencing and industrial image analysis as they offer scalable performance. They range from fanless NVIDIA® Jetson™ based solutions to high-end industrial servers and workstations with GPUs or AI accelerators and can be used for a variety of applications.
Here you can find a selection of possible basic systems and configurations.
Our team of experts will gladly assist you with individual requirements at any time.
Advantech MIC-733
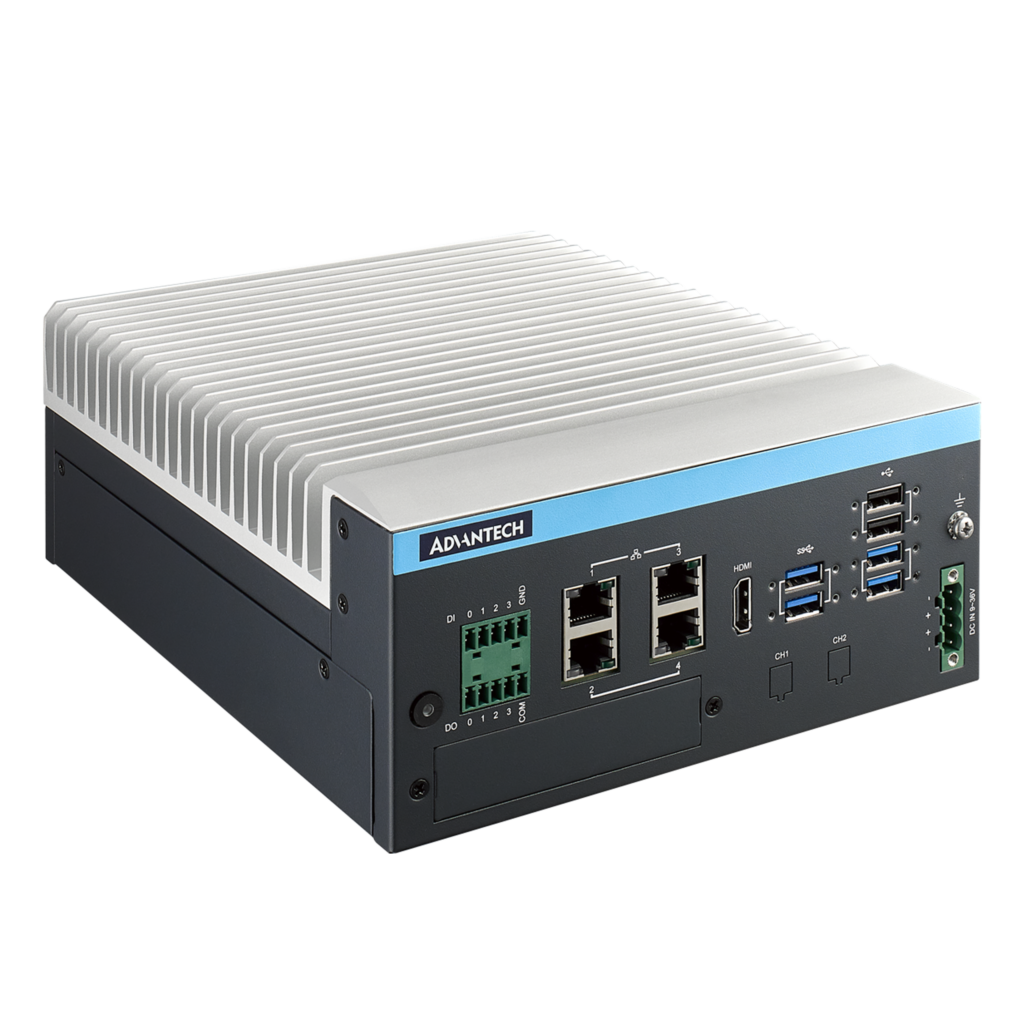
Advantech MIC-711
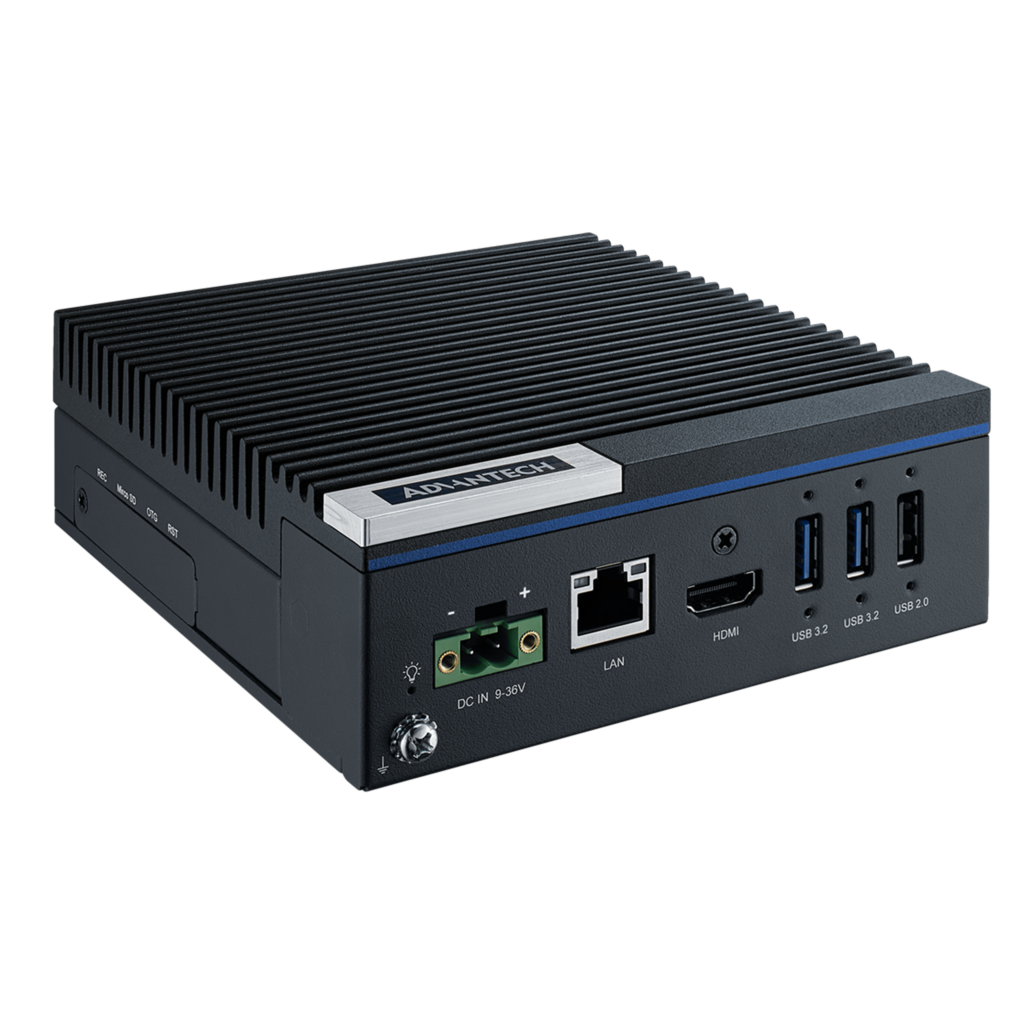
Advantech MIC-713
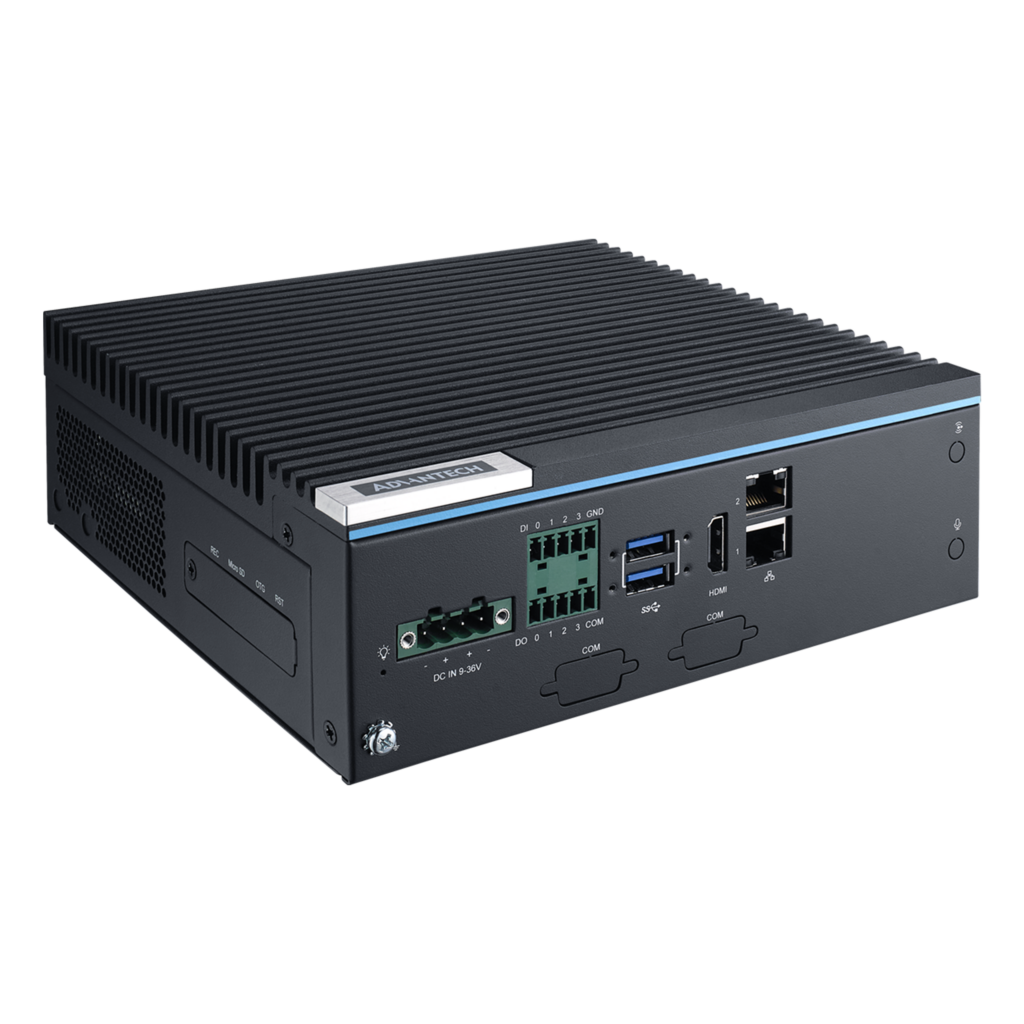
Advantech HPC-7420
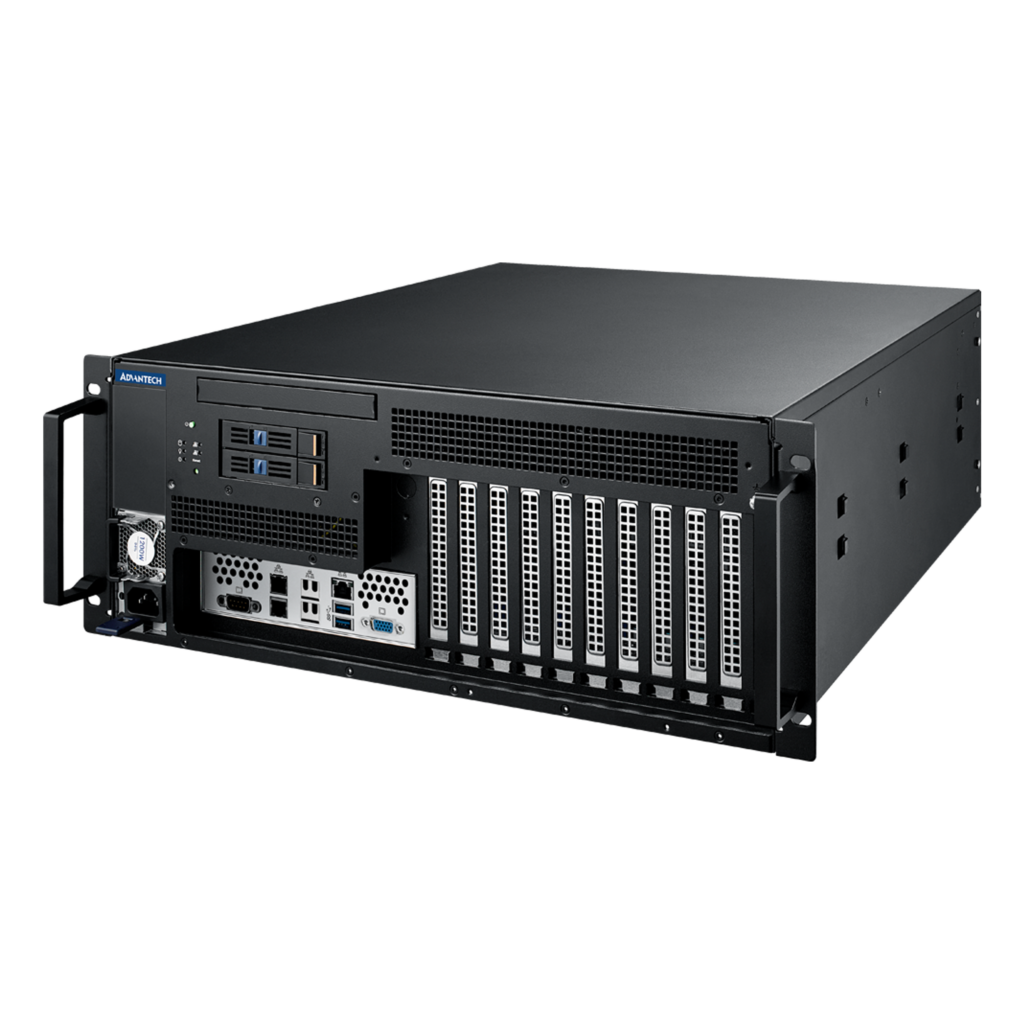
Advantech HPC-7485
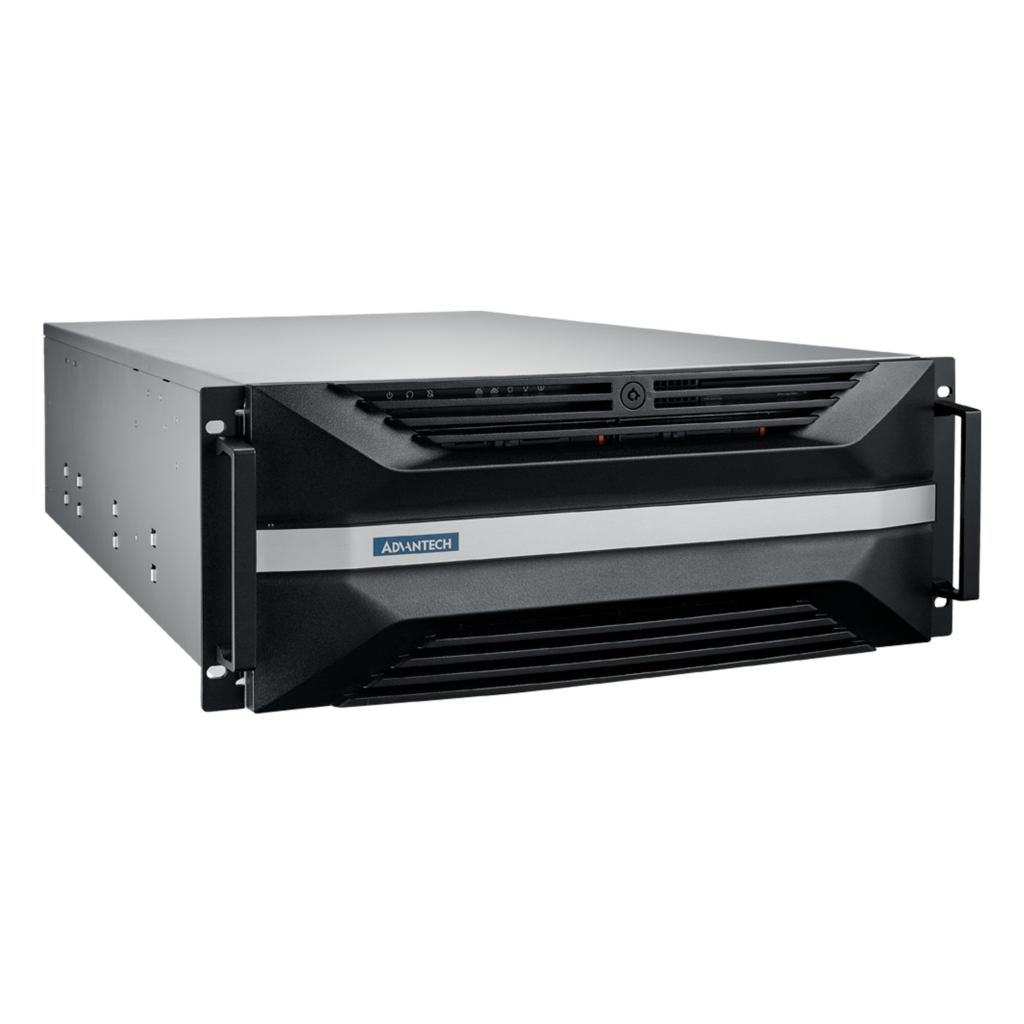
Devices
These pages could also be interesting for you.
Panel PCs
IoT-Gateways
Boards
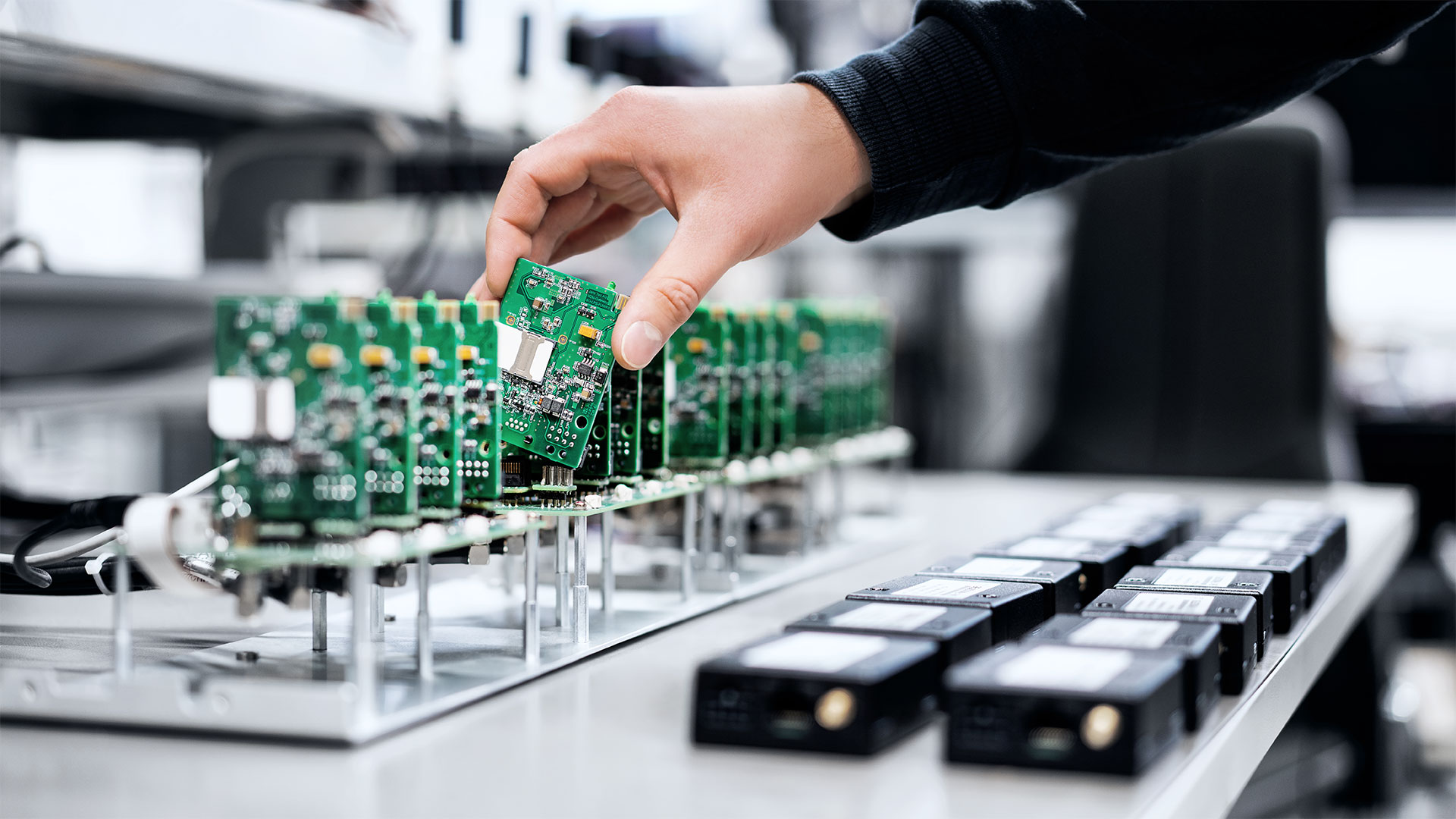
Advantages for companies: Industrial PCs as the key to increased efficiency and cost savings
Durability
With the selection of suitable hardware components, our industrial PCs are designed for demanding environmental conditions and are therefore ideal for applications with increased temperature requirements and mechanical stress. However, should a problem occur, we will of course be on hand to help you with our 40 years of hardware expertise.
Innovation
As one of the leading providers of industrial PCs and IoT solutions, we have been combining tradition and innovation for over 40 years. Janz Tec has certifications and awards that confirm a strong innovative strength, a clear digitalization strategy and the constant pursuit of sustainability goals.
Customization options
Our industrial PCs are suitable for different mounting options, including rackmount, wallmount, VESA mounting, booksize or with DIN rail (top-hat rail). This ensures uncomplicated use in a wide range of industrial environments.
Do you have special requirements for your IPCs? Whether it’s hardware, software or design – we will respond to your individual requirements and will be happy to advise you.
Areas of application: Industrial PCs are used in these sectors
Janz Tec hardware components have been in use in countless sectors and industries since 1982. Logistics, automation, electromobility and digital signage are just a few examples of the possible areas of application. Our computer systems are characterized by their particular versatility and flexibility.
Individual customization options for your industrial PC
If you have not found a suitable product for your requirements, please contact us. We offer individual customizations regardless of the quantity. In consultation with our team of experts, we will work with you to develop individual technical solutions that precisely meet your requirements.